Success for suction robot following trials inspecting aircraft for damage
- Like
- Digg
- Del
- Tumblr
- VKontakte
- Buffer
- Love This
- Odnoklassniki
- Meneame
- Blogger
- Amazon
- Yahoo Mail
- Gmail
- AOL
- Newsvine
- HackerNews
- Evernote
- MySpace
- Mail.ru
- Viadeo
- Line
- Comments
- Yummly
- SMS
- Viber
- Telegram
- Subscribe
- Skype
- Facebook Messenger
- Kakao
- LiveJournal
- Yammer
- Edgar
- Fintel
- Mix
- Instapaper
- Copy Link
Posted: 4 February 2019 | International Airport Review | No comments yet
Cranfield University has carried out successful trails of a suction robot which can detect and repair damage to aircraft, as part of the CompInnova Project.
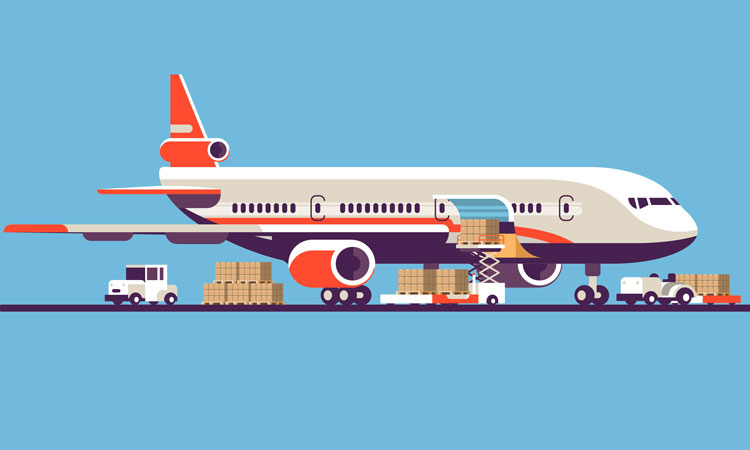
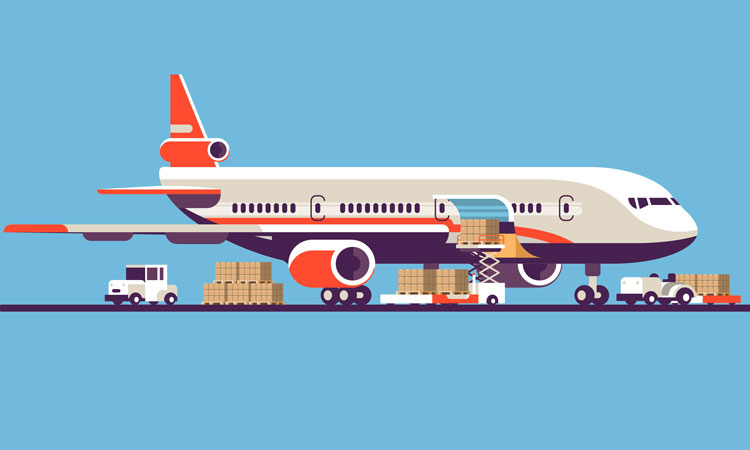
The four-wheeled Vortex Robot, developed as part of the CompInnova Project, was tested in field trials using Cranfield’s Boeing 737 and was able to stick to and move around the sides and underbelly of the plane.
The CompInnova Project aims to to develop a revolutionary automated multipurpose and multifunctional Vortex robot that, for the first time, will carry ultrasonic Phased Array (PA) and Infrared Thermography (IRT) equipment for inspecting metallic and composite aircraft structures respectively. The robots will also have installed a novel repairing system for the inspected damaged components. The aim of this achievement is to drastically improve the quality of maintenance procedures and reduce significantly its time and cost.
Structural inspection of aircraft components is currently done manually, making it time-consuming, subject to human error, and costly, with aircraft maintenance expenditure usually representing 20 per cent of overall operating costs.
Professor Iain Gray, Director of Aerospace at Cranfield University and Principal Investigator of the project, said: “There is an increasing use of composites throughout large and small aircraft structures. Developing new, efficient, modern ways to inspect those composites is a real key performance driver.”
Georgios Andrikopoulos, post-doctoral researcher at Lulea University of Technology, who is leading the development of the Vortex platform, said: “We successfully tested the capabilities of the robot prototype on all different surfaces of the aircraft, even the transition beneath the wing and fuselage. This is really challenging to accomplish because the robot will have to support a big payload in relation to its size.”
An autonomous version of the robot equipped with sensors for inspection and tools for repair is now being developed by the project team and could carry a payload of around nine kilograms, including ultrasonic and thermal imaging cameras for detecting damage, and a laser to remove and repair it.
The CompInnova Project involves five partners from across Europe and has received funding from the European Union’s H2020 Framework Programme.
Related topics
Aircraft, Airside operations, Engineering, Machinery, Regulation and Legislation, Risk Management Solutions, Safety
Related airports
Related organisations
Cranfield University, European Union (EU), Lulea University of Technology