Munich Airport test runs its first ever “evoBOT”
- Like
- Digg
- Del
- Tumblr
- VKontakte
- Buffer
- Love This
- Odnoklassniki
- Meneame
- Blogger
- Amazon
- Yahoo Mail
- Gmail
- AOL
- Newsvine
- HackerNews
- Evernote
- MySpace
- Mail.ru
- Viadeo
- Line
- Comments
- Yummly
- SMS
- Viber
- Telegram
- Subscribe
- Skype
- Facebook Messenger
- Kakao
- LiveJournal
- Yammer
- Edgar
- Fintel
- Mix
- Instapaper
- Copy Link
Posted: 23 June 2023 | International Airport Review | No comments yet
Developed at the Fraunhofer Institute for Material Flow and Logistics IML, the evoBOT now offers a first taste of this at Munich Airport.
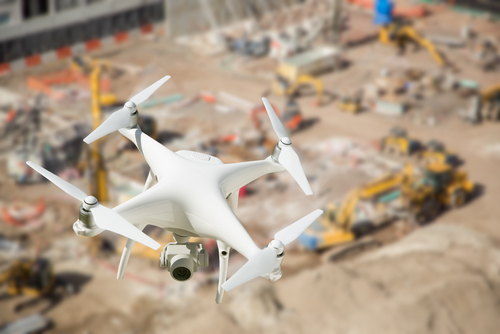
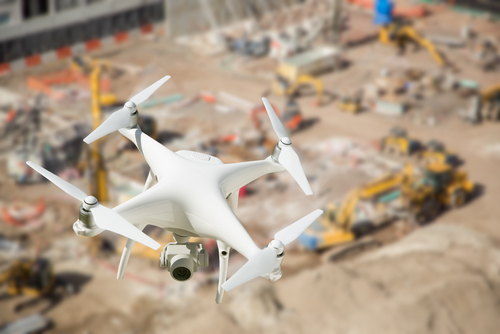
Drones are set to become a lived reality at Munich Airport.
Autonomous vehicles and robots are set to have a major impact on the future of air freight, and comes at a time of a shortage in skilled workers. Developed at the Fraunhofer Institute for Material Flow and Logistics IML, the evoBOT now offers a first taste of this. With its two wheels and gripper arms, the robot – which keeps itself perfectly balanced – mastered a first practical test in the cargo terminal and on the apron of Munich Airport.
Air freight is currently undergoing a profound transformation. Despite a shortage of skilled workers, high throughput rates have to be managed, while digitalisation is advancing at an ever faster pace. The evoBOT provides an initial response to this development. During its first test runs at Cargogate at Munich Airport, the autonomous robot proved how versatile it is. “The development and expansion of the cargo and logistics sector are essential components of our corporate strategy. We welcome every initiative to optimise and digitalise handling processes. The evoBOT will facilitate the day-to-day work of our employees in the cargo area and make the workplace more attractive”, explains Jost Lammers, Chief Executive Officer of Munich Airport.
“Our evoBOT is the beginning of a new population of autonomous vehicles and robots. With its arms and the fact that it moves on two wheels, it represents a step on the path to the humanoid future of robotics. The practical test carried out at Munich Airport impressively underpins the potential of this development. The evoBOT can work as a fellow colleague in a wide range of applications”, emphasises Professor Michael ten Hompel, Managing Director of Fraunhofer IML.
The dynamically stable transport robot developed by Fraunhofer IML is particularly characterised by its arms and the adaptive load pickup made possible by them. It can take on a wide range of tasks such as handling hazardous goods, transporting parcels for longer recurring distances, relieving employees during lifting and overhead work, procuring materials or even providing support during the loading and unloading of aircraft. Despite its load capacity, the evoBOT is exceptionally agile on its two wheels. It can reach a maximum speed of up to 60 km/h and transport a load of up to 100 kg. It can operate either alone or with others. Thanks to its good maneuverability, the evoBOT can be operated in various areas both indoors and outdoors. Its low carbon footprint also contributes to its diverse use.
“Against the backdrop of rising air freight figures and the challenges of recruiting employees, we are very pleased to be able to take a look into the future with Fraunhofer IML. Into the very near future at that”, adds Claudia Weidenbusch, Managing Director of Cargogate Munich Airport GmbH.
The Digital Testbed Air Cargo (DTAC), in the context of which the current test was carried out, and the initial development of evoBOT are funding programmes of the German Federal Ministry for Digital and Transport (BMDV). In addition to Cargogate Munich Airport GmbH and Fraunhofer IML, the DTAC project consortium includes nine other partners from research and industry: CHI Deutschland Cargo Handling GmbH, Flughafen Köln/Bonn GmbH, Frankfurt University of Applied Sciences, Fraport AG Frankfurt Airport Services Worldwide, Lufthansa Cargo AG, LUG aircargo handling GmbH, Mitteldeutsche Flughafen AG, Schenker Deutschland AG and Sovereign Speed GmbH.
Related topics
Airport development, Autonomous Technology, Communication Technology, Digital transformation, Drones, Operational efficiency, Robotics
Related airports
Related organisations
CHI Deutschland Cargo Handling GmbH, Flughafen Köln/Bonn GmbH, Fraport AG Frankfurt Airport Services Worldwide, Fraunhofer IML, Fraunhofer Institute for Material Flow and Logistics IML, Lufthansa Cargo AG, LUG aircargo handling GmbH, Mitteldeutsche Flughafen AG, Schenker Deutschland AG, Sovereign Speed GmbH.