The importance of coordinating your ground support
- Like
- Digg
- Del
- Tumblr
- VKontakte
- Buffer
- Love This
- Odnoklassniki
- Meneame
- Blogger
- Amazon
- Yahoo Mail
- Gmail
- AOL
- Newsvine
- HackerNews
- Evernote
- MySpace
- Mail.ru
- Viadeo
- Line
- Comments
- Yummly
- SMS
- Viber
- Telegram
- Subscribe
- Skype
- Facebook Messenger
- Kakao
- LiveJournal
- Yammer
- Edgar
- Fintel
- Mix
- Instapaper
- Copy Link
Posted: 12 August 2016 | Diego Alonso Tabares (Airbus) | No comments yet
Diego Alonso Tabares, Senior Engineer – Airport Operations at Airbus, provides an overview of the innovative European Commission-funded INTERACTION project, which was launched to help evolve airport operations to develop fully integrated and coordinated management of the processes that converge into aircraft turnaround.
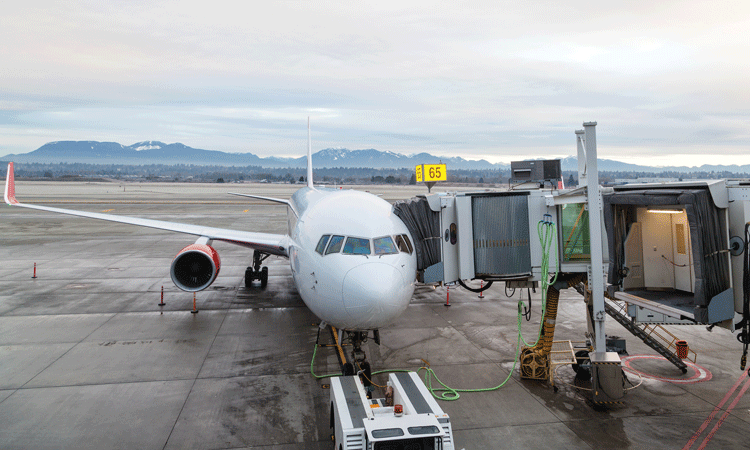
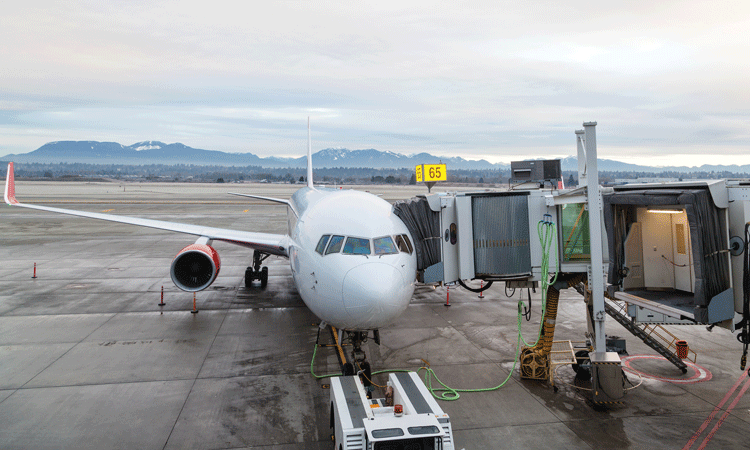
The airport community is well aware of the multiple challenges that airports worldwide are facing today – including complexity, information flow and stakeholder management. A solution to cope with this complex environment for day-to-day operations is the use of Collaborative Decision Making (CDM).
Looking specifically at ground handling operations it’s important to get all stakeholders – airports, airlines, ground handlers, aircraft and ground equipment manufacturers – together, but gathering such a wide representation to establish the day-to-day knowhow for a research topic is a huge task. Nonetheless, it was a task that we managed to achieve when the INTERACTION project consortium launched in October 2013.
We drew upon our own experiences in the sector to come up with more than 40 solutions, which were then explored, analysed, checked for feasibility and cost benefit analysed. The most promising solutions have been developed, mocked up and tested in a controlled – and even operational – environment. As the project draws to a close it’s interesting to see what has been achieved:
Automated docking of Ground Support Equipment (GSE) to aircraft
For every GSE that docks to an aircraft – such as boarding bridges, cargo loaders, catering trucks and belt loaders – an operator is required to drive the GSE. This docking operation is subject to human error and variability. In order to improve the current situation we proposed targets around aircraft doors that can be used by the GSE to provide guidance to the driver or even to create fully automated docking.
Due to differences with the equipment in use, there isn’t a single technology that would fit all GSE, so the design of the target and its exact position relative to the aircraft door is being developed as an industry standard with the option to retrofit in mind for existing GSE.
Furthermore, real tests have been carried out to assess the versatility of the concept using different technologies including optical cameras, infrared and also having the targets on aircraft airframe, which is useful for GSE that is docked manually.
Aircraft navigation lights powered by towbarless tractors
Aircraft maintenance towing – or positioning towing (from parking stand to hangar, or moving between different parking stands) – requires the aircraft to have its navigation lights on. From a practical point of view this requires the aircraft auxiliary power unit (APU) to be on or for the tractor to be equipped with a mounted ground power unit (GPU), as maintenance towing can last typically an hour and aircraft batteries alone may not cope with all the systems needed for this operation.
During the project an interface between the towbarless tractor and Airbus aircraft were developed to supply 115V AC/ 28V DC directly from the tractor to the aircraft which enables the navigation lights to be powered directly, therefore reducing the need to have the APU on. This also resulted in less maintenance, fuel and emissions. This solution has also been tested on the A330, A350XWB and A380 in operation.
Aircraft turnaround time management
Airports around the world all want to have full visibility of what is going on at the terminal and on the apron. The link between those in the aircraft environment and the turnaround process is often missing.
During the INTERACTION project, all stakeholders’ requirements were gathered and a real prototype with input automation including the aircraft turnaround activities, timestamps, and decision-helping processes has been developed.
The centralised turnaround information management platform developed in INTERACTION integrates information from different airport processes – such as aircraft, passenger or baggage – and increases the information sharing between all airport stakeholders. It provides a great improvement in common situational awareness, as well as a performance management tool that raises warnings and alerts when one task steps out of schedule and a collaborative decision making tool that helps solve events in real-time.
This prototype has been tested in Athens airport in full operational mode.
It is of utmost importance to highlight the full commitment of all the INTERACTION consortium members as fundamental to the project’s success and goals achieved. So now that the project is coming to an end what is next? What can we do to continue the CDM for the success of tomorrow’s airports? Your ideas and support are always welcomed.
About INTERACTION
Launched in October 2013, INTERACTION (INnovative TEchnologies and Researches for a new Airport Concept towards Turnaround coordination) is a European Commission FP7 project which aimed to propose new procedures, technologies and tools for enhancing time-efficient turnaround airport operations by looking for improvements in each process individually, as well as in an overall coordinated way.
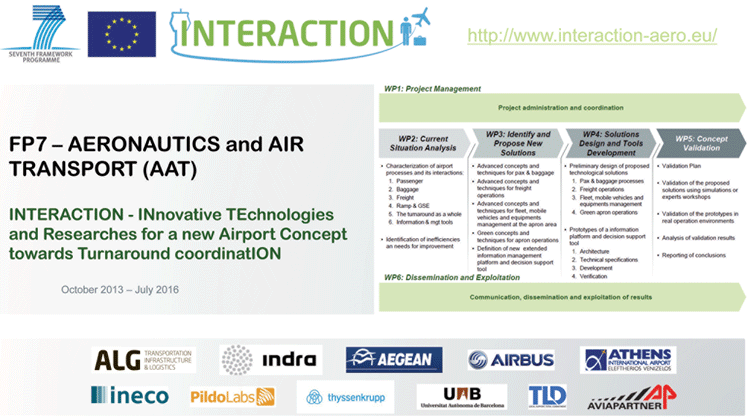
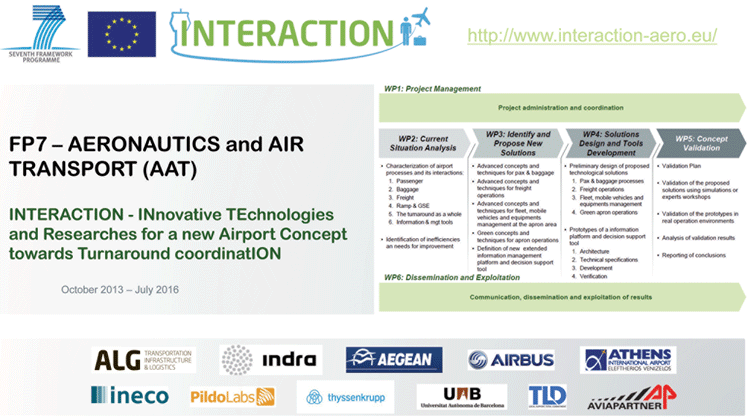
The INTERACTION project and consortium members
The common goals were to minimise the global turnaround time and to reduce the effects of perturbations that may appear in any of the airport sub-processes during turnaround. This research extends to the ground-side existing concepts developed for the airside in related European research programmes such as SESAR. The project solutions are structured in five knowledge groups:
- Airport terminal operations – advanced concepts and techniques for time efficient passenger and baggage processes
- Air freight operations – advanced concepts and techniques for time efficient freight operations
- Ramp operations – advanced concepts and techniques for fleet, mobile vehicles and equipment management in the apron area
- Green concepts – green concepts and techniques for apron operations
- New tool developments – definition of a new extended information management platform and decision support tools.
You can find out more at: www.interaction-aero.eu
Diego Alonso Tabares has a MSc Aeronautical Engineering. He has worked in Airbus since 2003, first for A380 entry into service preparation and then for aircraft-airport integration issues for in service, in development and future projects aircraft. Diego holds several positions in international committees for Aircraft Ground Equipment.
Issue
Related topics
Airside operations, Ground handling, Sustainability, Terminal operations