Keeping Riga International Airport flying through the fog
- Like
- Digg
- Del
- Tumblr
- VKontakte
- Buffer
- Love This
- Odnoklassniki
- Meneame
- Blogger
- Amazon
- Yahoo Mail
- Gmail
- AOL
- Newsvine
- HackerNews
- Evernote
- MySpace
- Mail.ru
- Viadeo
- Line
- Comments
- Yummly
- SMS
- Viber
- Telegram
- Subscribe
- Skype
- Facebook Messenger
- Kakao
- LiveJournal
- Yammer
- Edgar
- Fintel
- Mix
- Instapaper
- Copy Link
Posted: 29 May 2015 | Dzintra Jātniece, Jānis Maslovskis, Sandra Lāma, Vladimirs Krasausks | No comments yet
With an ageing lighting system causing visibility problems at Riga International Airport, the time had come to invest in a major upgrade to bring it up to CAT II standard. However, the single runway airport, the busiest in the Baltic region, – had to remain fully operational. Dzintra Jātniece, Director – Airfield Management Department and colleagues describe how it successfully introduced the upgrade.
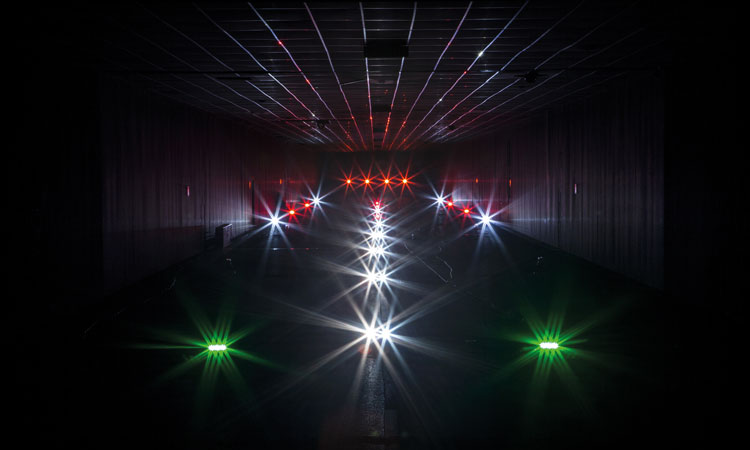
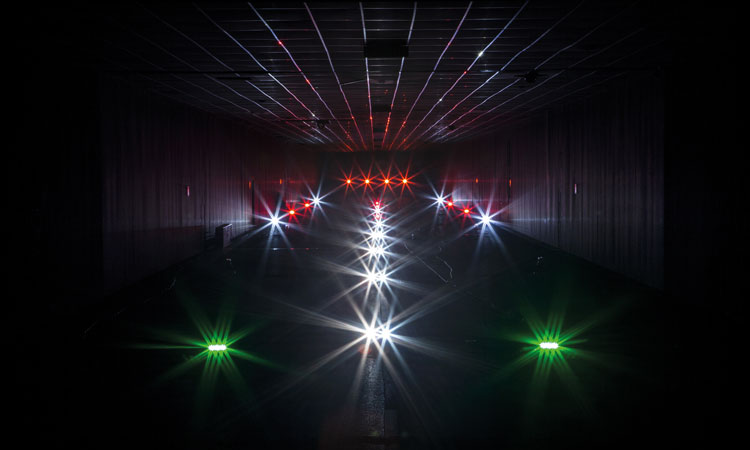
Riga International Airport is the largest airport in the Baltic States and handles almost five million passengers on 75,000 flights annually. The airport was built in 1974 as a joint use civil and Soviet military airfield. After the collapse of the Soviet Union in 1991, the newly established SJSC Starptautiskā lidosta ‘Rīga’ received the worn-out airfield infrastructure.
The first significant reconstruction work was pavement reconstruction of the concrete runway and the main taxiways as well as construction of the aerodrome lighting system in 1993. Further reconstruction works focused on the development of the terminal building. In 2004, Latvia joined the European Union and a rapid increase in the number of flights and passengers began, further facilitated by the introduction of low cost carriers to the airport. From then on, the development of the airport’s infrastructure has been a constant challenge.
In spring and autumn during foggy weather, the runway visual range (RVR) often falls below the 550m mark, which at the time resulted in approximately 10% of all daily flights being diverted to alternate airports. It was also possible for fog to influence airport operations two days in a row, causing great losses to the airlines and the airport alike. In 2007, the necessity for infrastructure development was raised again, so that the airfield could be certified according to CAT II precision approach requirements. This touched upon not only the aerodrome lighting system, but also the radio navigation aids which are owned and managed by the ATS provider, SJSC ‘Latvijas Gaisa Satiksme’.
In 2008, the runway was extended, but as pointed out by supervising institutions, important infrastructure reconstruction work was still necessary. There was not enough funding at the time, but after carrying out preliminary work, all instrument lighting systems (ILS) were replaced by new systems capable of up to CAT III certification in the first part of 2008.
In 2010, the airport began implementing the EU project: ‘Development of Infrastructure of the Riga International Airport’ by attracting funds from the Cohesion Fund. This allowed it to carry out the grandest airport reconstruction work not only in the history of Riga airport, but also in all of the Baltic States.
The planning and development of the technical and economic feasibility study started in 2009. Although the preliminary design work and the technical project were developed in record time (only 12 months), during project development, airport staff and the project authors faced a daunting task – having to solve engineering puzzles and work time conflicts between the airport and the construction work with respect not only to regulatory documents, but also the budget.
Widespread renovation
Renovation of the runway pavement, improvement of the aerodrome lighting system according to CAT II requirements, installation of taxiway centre line lights and transition to a new aerodrome lighting control system all had to be carried out within the framework of the project. Runway strip reinforcement, construction of two new taxiways, full reconstruction of two main aprons, construction of a new de-icing platform, full reconstruction of a rainwater and drainage system and construction of two technical hangars for washing of airfield equipment and waste collection also had to be carried out. And all of this had to be done at one operational airport with a single runway. Incidentally Riga is the only international airport in the country and the largest in the Baltic region.
Construction work was scheduled to begin in 2012, but, due to complications with the tender process, the start of construction work had to be postponed to 2013.
There were numerous challenges during the execution of the project as a whole and this article will shine a light on a few of those in relation to the lighting system.
The most noteworthy challenge was scheduling runway top layer pavement change together with inset lights. The pavement was reconstructed in 75m chunks – with, every chunk included up to six existing centre line lights, up to 12 taxiway centre line lights at intersections, and up to 18 touchdown zone lights. As the airport closed down each night at midnight, the maximum time for replacing one chunk was six hours. This included four hours for actual work and two hours for asphalt cooling and marking renewal, ready to let the first flight take-off at 06:00AM.
The existing runway inset lighting systems were NOTAMed, i.e. unserviceable for the period of the execution of this work. Cabling for the new lights was installed beforehand and the contractor was confident about this part of the work. The actual light fixtures were installed on the following nights. The most risky part of this work was removing the existing inset lights, as these were installed more than five years earlier by another contractor. No one was sure of the actual depth of cabling, meaning that any of the centre line light cables could be damaged during asphalt milling, with almost no time for repair, as the new layer of asphalt was already waiting in the queue to be paved. This required perfect coordination between several otherwise independent teams of experts in a very time constrained environment, as well as a clear contingency plan in case any of the cables got damaged.
LED integration
Another challenge was the integration of the new locally controlled LED lighting system with the existing lighting system. For example, the existing incandescent taxiway edge lights had to be installed in one line with the new LED lights. Contractors were faced with several difficult tasks here. The problems started with the existing cabling and ducting as it turned out that there was not enough space in the existing pipes and chambers. Next, the colour and intensity of the incandescent blue and the LED blue turned out to be completely different. This resulted in complaints from pilots and clearly needed to be adjusted.
As mentioned, the scope of the work also included full replacement of the airfield ground lighting (AGL) management system. Although this sounds simple in theory, the reality was that it had to be done over one night so that aircraft movements the next morning would not be affected in any way. Furthermore, ATC controllers had to be fully trained and aware of the new software as they were the ones using the system most. In the end this turned out to be less of a technical challenge than expected and more of a human cooperation challenge. The different parties involved (ATC, the general contractor and the AGL subcontractor) each had different goals and perspectives, meaning the airport authority had to play the intermediary role of ensuring everybody was happy and the system worked.
Main reconstruction works at the airfield were finished on 6th October 2014. Preparation of documents for airfield certification and training of employees for the new procedures that meet the requirements of CAT II had already been launched. After the certification, aeronautical information was published, becoming effective as of 5th March, 2015.
Since Riga International Airport became a CAT II aerodrome, no flights have been redirected to alternative airfields due to weather conditions. However, the work continues, as during 2015 reconstruction of Apron 1 will be completed, and new specialised fire and aviation rescue vehicles and equipment for security measures will be purchased. The project is to be implemented by 31st December 2015.
Biographies
Safety on the ground? Yes please!
Everybody is talking about safety for passengers and crew in the air. What about safety on the ground? Intelligent safety systems combine the tasks of monitoring and controlling lights on runways and taxiways into a comprehensive system – and they ultimately help to prevent a high percentage of accidents on the ground where most accidents happen. Combined with LED equipped taxiways and runways, the safety situation at airports worldwide can be improved extraordinarily. Intelligent safety systems and LED lighting in general are two of the most important future topics for airports – and they were part of the agenda during the HELLA Airport Lighting Day in Lippstadt, Germany.
On 24th April 2015, international lighting professionals from Canada, Germany, the Netherlands, France, Egypt and more discussed the latest technologies and developments in airfield lighting with experts from HELLA – a pioneer in the LED technology sector. What is new? What is relevant for the future? During a lively discussion in the conference room, ideas and suggestions were exchanged. Later the complete production line including the 100% testing philosophy was shown and guests had the opportunity to experience various details of the HELLA LED lights hands-on in an interactive market place. The participants were able to get the best impression of LED lighting by exploring and seeing it for themselves.
As LED lighting has already reached the industry and more and more airports have decided to convert, HELLA is making use of its existing knowledge of over a hundred years to transfer the technology to other industries. What started originally with the development of vehicle lighting is now part of ordinary life in many areas – the quick changeover to a lighting system that meets the global ecological challenge and the economic requirements of the time with the greatest possible efficiency.
LED lighting offers numerous safety benefits for airports. The clear colours and brilliant intensity of the lighting ensure an optimal view even during poor weather conditions; providing pilots with clear definition between the taxiway, stop bar and runway lights, ensuring a safe landing. These are some of the reasons why more and more progressive airports have chosen LED lights – as airport professionals confirm.
The discussions about increased safety with new lighting technologies then led to further discussions about intelligent safety systems. One version of an intelligent safety control system will be shown by HELLA at the inter airport Europe event, taking place from 6-9 October in Munich.
The last highlight of the full day workshop was a presentation in the 140m HELLA light testing facility. The professionals were shown HELLA’s latest product: the LED inset approach light in LED. The company is one of the few airfield companies worldwide who can provide LED inset approach light technology. The product is shortly going into series production, and the flashing variant is already in the industrialisation phase.
The latest installations of HELLA have been realised in Dubai, UAE (one runway completely upgraded to LED technology with around LED 12,000 lights and around 800 sign kits), Vancouver, Canada (one runway completely upgraded to LED technology with 1,500 lights) and Paris, France (one runway completely upgraded to LED technology with around 800 lights). SFL Systems have also been installed in Copenhagen, Denmark: Stavanger, Norway; and Wunopito, Indonesia. The company is currently working on several large projects in the Middle East, North America and Europe. Upcoming projects are planned to be realised in Egypt and Columbia. www.hella.com
Issue
Related topics
Airfield lighting, Airport development, Airside operations, Safety