Munich Airport: Innovative and sustainable
- Like
- Digg
- Del
- Tumblr
- VKontakte
- Buffer
- Love This
- Odnoklassniki
- Meneame
- Blogger
- Amazon
- Yahoo Mail
- Gmail
- AOL
- Newsvine
- HackerNews
- Evernote
- MySpace
- Mail.ru
- Viadeo
- Line
- Comments
- Yummly
- SMS
- Viber
- Telegram
- Subscribe
- Skype
- Facebook Messenger
- Kakao
- LiveJournal
- Yammer
- Edgar
- Fintel
- Mix
- Instapaper
- Copy Link
Posted: 4 April 2016 | Philipp Ahrens, Director of the Satellite Project Team, Munich Airport | No comments yet
Munich Airport’s €900 million Satellite Terminal project – which is set to increase capacity at the airport by 11 million passengers while generating 40% less CO2 emissions than existing terminal buildings – is now entering the final stages of completion. Philipp Ahrens, Director of the Satellite Project Team, reveals the airport’s innovative and sustainable terminal system…
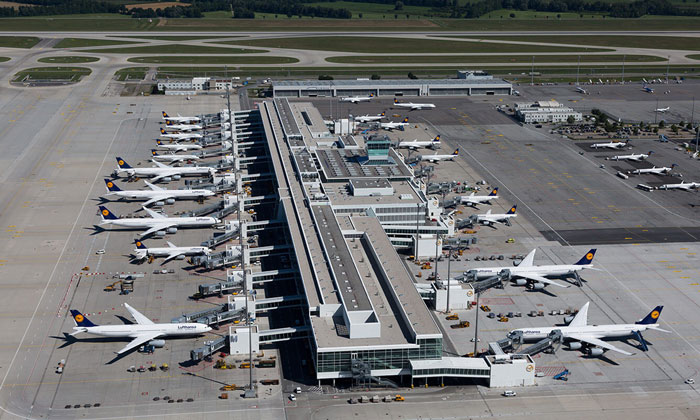
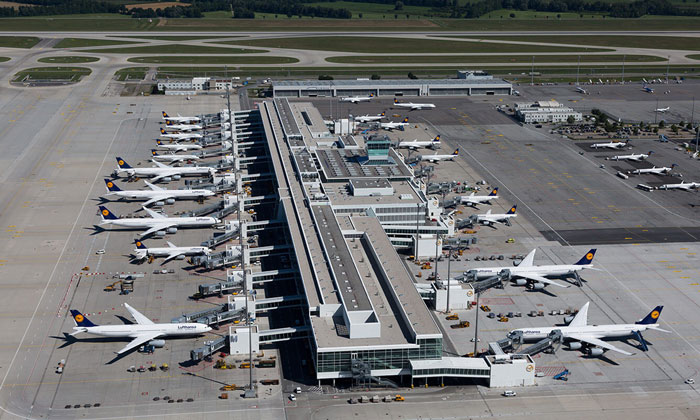
Munich Airport’s new Satellite Terminal is now in the final stages. Construction commenced in April 2012 and the terminal will be ready for operation by 26 April 2016. The building is being constructed to the east of Terminal 2 and will increase capacity by 11 million passengers, including housing 27 contact stands for Lufthansa and their Star Alliance Partners. The construction of the building is finished and the interior is currently being fitted – mainly the retail and gastro units.
In the meantime the testing of the underground passenger transport system, located underneath the apron, is ongoing. The fullyautomated transport system, APM 300, provided by Bombardier, connects the two buildings and will have a capacity of 9,000 pass engers per hour and direction. A maximum of three trains of four carriages will serve all three different passenger types with two carriages for Schengen passengers, one carriage for non-Schengen and one carriage for non-EU arrival passengers.
Additionally, the apron layout has been adapted to the needs of the new stand layout around the building. The ‘Operational Readiness Program’ (ORAT) commenced in November 2015 with 32 trial days (two per week) out of which internal trials were carried out until Christmas. Since January 2016 external trial passengers were invited to join in as well to test the processes.
The vision for Munich Airport’s development began in the late-1990s, when Munich Airport and Lufthansa signed a MoU to create a joint venture – The Terminal 2 Management Company (with a 60/40% split) – and started jointly financing, planning and constructing Terminal 2 as a dedicated Lufthansa / Star Alliance Terminal. This success story, which is still unique in Europe, proved to be a good decision as Terminal 2’s nominal capacity of 25 million passengers has now been exceeded four years in a row and clearly indicates the urgent need for additional capacity on the ground. When constructing Terminal 2, the next construction phase – the Satellite – had already been considered in the planning process.
The Satellite is a mid-field building and is separated by three parallel taxiways from Terminal 2. The tunnels under the apron that connect the Satellite with Terminal 2 will be used for the passenger transport system and to transport baggage between the two buildings. These tunnels were built during the construction of Terminal 2. The baggage sorting system in the east of Terminal 2 was constructed in a way that enables it to be the future baseline for the Satellite building.
The natural progression was to once again jointly finance, plan and construct the new Satellite building with the Terminal Management Company acting as the constructor. The budget for the Satellite Terminal – including the extension of the apron layout and the modification of the baggage sorting system – is approximately €900 million. The next extension is already in the planning process: a ‘T-stick’ towards the east, which will allow capacity for an additional six million passengers.
Given that the capacity limit of 25 million passengers has been reached in Terminal 2 for the fourth consecutive year there is already an urgent need for further capacity. Another important goal, however, was to increase the quality for passengers, especially when boarding or de-boarding. This was achieved by creating 27 additional contact stands. The building was planned and constructed to be fully flexible and able to serve all types of traffic (Schengen, non-Schengen and non-EU arrival traffic) on three different levels, following the same philosophy as Terminal 2. Since the Terminal 2 system is exclusively reserved for Lufthansa and its Star Alliance partners, the Satellite building aims to provide seamless transfer processes.
The Satellite Terminal will also feature the so-called ‘remote collecting gates’. From a total of six gates on level 3, passengers from Schengen origins to Schengen destinations with tight connecting times can be driven with separate buses from the Satellite to a remote position in order to secure connecting flights and improve the overall transfer quality.
Nineteen retail areas will invite passengers on both departure levels to shop and the Satellite will complement Terminal 2’s luxury brands by focusing on premium brands. A change between shopping areas in Terminal 2 and the Satellite is possible via the passenger transport system at any time.
Free ‘work and relax zones’ plus generous family areas will improve passengers’ waiting time and provide ample opportunity to recharge mobile devices. Full Wi-Fi connectivity in the waiting area will allow for permanent connection to the rest of the world.
The Satellite will have a digital commercial concept: selling commercials on digital media walls to investors by a 3D animated walkthrough the building. This will give the customer a better feeling for their product placement within the building.
Of course the new market place area surrounding the apron tower will be the commercial heart of the building, reflecting not only the city of Munich but also Bavarian culture.
Our overall aim is to continuously improve our services for the airlines and their passengers. The new Satellite will definitely maximise convenience for the guests because the 27 new contact stands will offer easy excess from the gates. Passengers who start their journey from the Satellite therefore do not need a bus transfer to reach their aircraft which means they have yet more time to enjoy this fascinating building and indulge in the large variety of attractive shops and restaurants.
Besides improving services for passengers and airlines the new Satellite Terminal also sets new environmental and energy efficiency standards. The very latest building materials and innovative heating, cooling and lighting technologies will ensure that energy usage is reduced to a minimal level: CO2 emissions generated by the building will be 40% lower than those emitted by the airport’s existing terminal buildings. Contributing to this reduction are the ‘climate façades’, found on the longitudinal sides of the building, which enable passengers (via escalators) to change between the building’s three passenger levels. These 4.5m-wide spaces separate the heated or cooled building proper from the open air and act as an accessible climate buffer. The façade is made of a newly-developed type of glass that allows daylight through but which – by means of a special coating – keeps out solar radiation, including heat.
The heating and cooling of the Satellite Terminal is achieved by use of the airport’s heating and cooling systems, with the necessary energy being generated by the airport’s own CHP (combined heat and power) plant, recently renovated with expanded capacity. Utilising this, the airport produces around 60% of the power it needs. The resulting waste heat is used for heating at cold times of the year and for cooling in summer, after being converted in an absorption refrigeration unit. Primarily the heating and cooling of the Satellite Terminal building is via underfloor conduits. Ventilation occurs via displacement ventilation technology and (external temperature permitting) naturally, via special openings in the building. The use of an innovative lighting concept – LED lamps – also offers further energy-saving potential as these lamps can be individually dimmed in accordance with lighting requirements and are laid out in such a way to have optimal effect.
The climate protection in the Satellite Terminal does not stop at the outer walls, though. All aircraft positions will be equipped from the start with so-called ‘Pre-Conditioned Air Units’ (PCA), via which Lufthansa and its partners’ aircraft can be heated by means of the airport’s heating network or cooled in the summer by the building’s own air conditioning system. The use of the aircraft’s own kerosene-powered auxiliary power unit is therefore superfluous, leading to a reduction in noise as well as of CO2 emissions.
Biography
Philipp Ahrens has 19 years experience within Airport Management in the fields of passenger and terminal management, ground handling, consulting, acquisition of international projects and traffic operations management at Munich Airport. He also worked for the Airports Council International Europe in Brussels for four years (between 2008-2012). Philipp holds an LLB in European Law of the University of West London as well as an Aviation MBA of the Danube University Krems, Austria. Since July 2012, Philipp has been Munich’s Director in charge of the Satellite Project within the Terminal 2 Management Company.