Building a new Baggage Logistics Centre in a fully operational airport: A challenge accepted by Geneva
- Like
- Digg
- Del
- Tumblr
- VKontakte
- Buffer
- Love This
- Odnoklassniki
- Meneame
- Blogger
- Amazon
- Yahoo Mail
- Gmail
- AOL
- Newsvine
- HackerNews
- Evernote
- MySpace
- Mail.ru
- Viadeo
- Line
- Comments
- Yummly
- SMS
- Viber
- Telegram
- Subscribe
- Skype
- Facebook Messenger
- Kakao
- LiveJournal
- Yammer
- Edgar
- Fintel
- Mix
- Instapaper
- Copy Link
Posted: 18 July 2022 | Sara Branco | No comments yet
Sara Branco, Baggage Handling Expert at Geneva Airport, tells International Airport Review about the airport’s new state-of-the-art Baggage Logistics Centre, which is expected to open by the end of 2023.
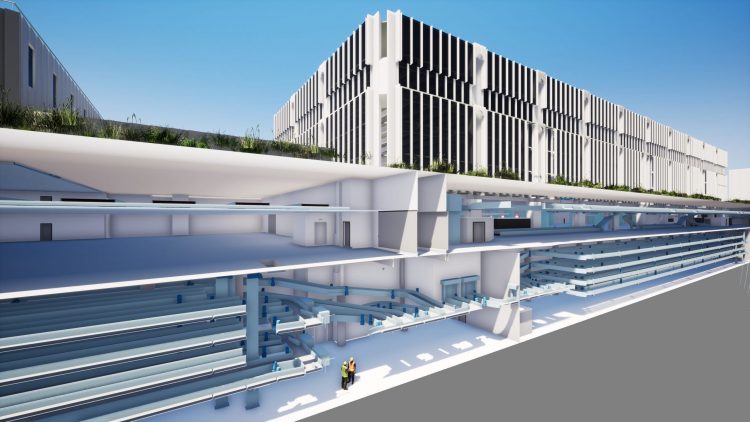
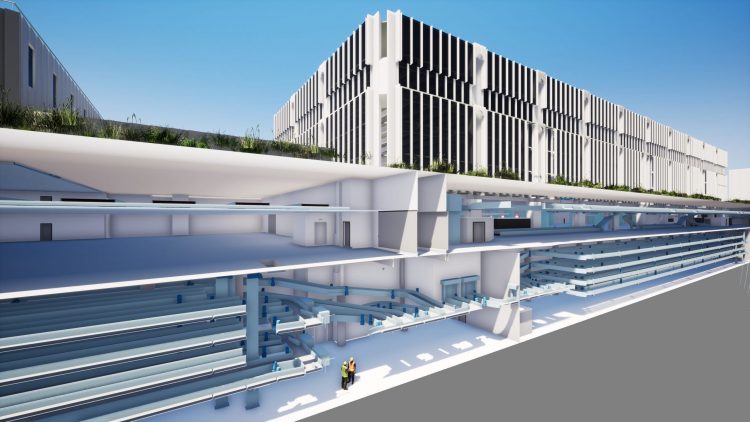
New building built to receive the new EDS standard 3 and conduct security screenings. Credit: Geneva Airport.
Geneva airport has 100 years of history, celebrated in 2020. From what was formally known as “champ d’aviation”, to a fully functional international airport. The increasing volume of passengers and goods matches the history of aviation, as well as the developing environment of the city itself. Geneva became the main home of different organisations that helped to put our airport into the spotlight for many years.
Following its growth, Geneva Airport has responded actively and presently to all demands and compliances of the Helvetic Confederation, France, IATA, airlines, and ground handlers. A strong, liable, and trustworthy relationship between all parties has been built and it allows us to face all challenges that airports face nowadays; one of which is the IATA resolution 753. It is common knowledge that the current scanners (standard 2) will no longer meet the new requirements for screening hold baggage, and that we need to comply with European standards regarding security by installing the latest-generation scanners (EDS standard 3).
Genève Aéroport put the foundation stone in place for its new Baggage Logistics Centre on 26 September 2019. It is a high-performing, innovative and more environmentally friendly Baggage Logistics Centre and is expected to open by the end of 2023. The current system, the main sorting system, for example, has been in use since 1994, and therefore needs to be replaced. This project also involves the replacement of all check-in desks, belts, conveyers, and scanners, which means that all processes to operate the brand-new system need to be built and replaced. The challenge? Make all the replacements while the current system is still operating! What does this mean? It means that, due to the unique location of Geneva Airport, there is no solution to develop this project elsewhere than where it is already placed.
Several challenges, such as infrastructure, were identified while the project was still a case study, but the operational challenges had an impact on the workflows, information plan, the internal communication and the problem‑solving process. There was no better excuse for exercising our creativity, amplifying our knowledge and stimulating our teamwork. The right ingredients to exercise great management from the operations point of view…
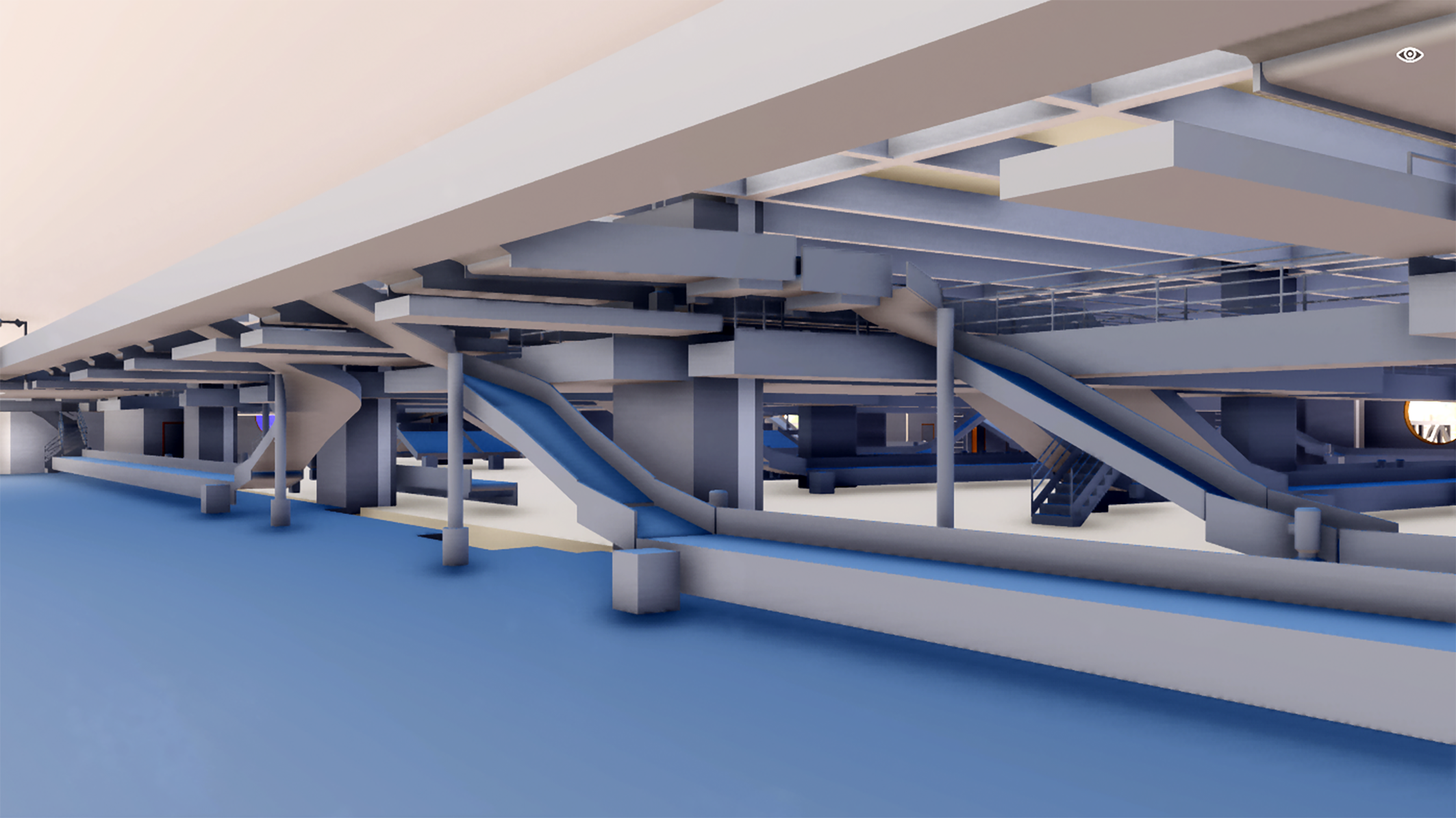
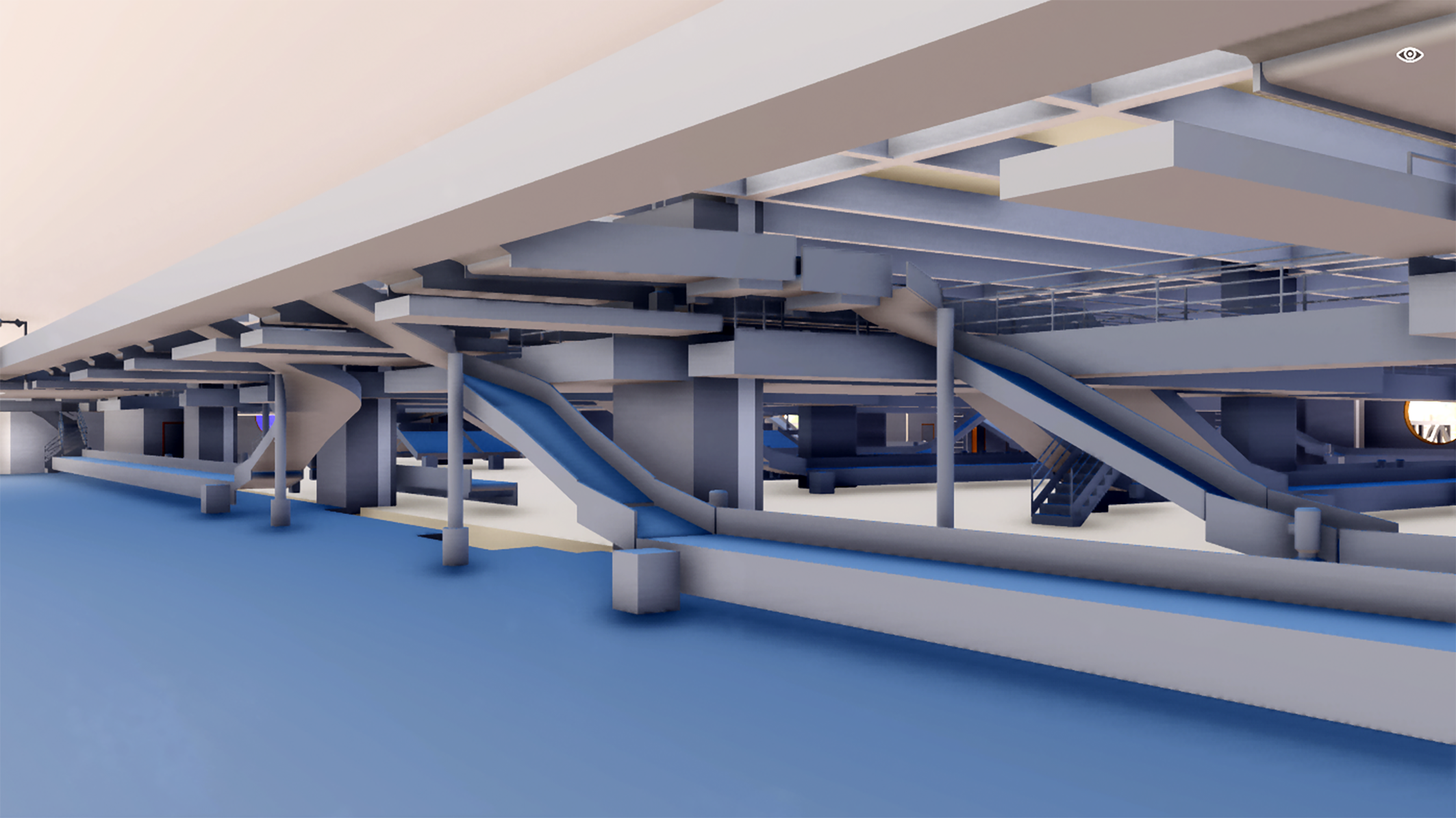
New arrival terminal with baggage retrieval area. Credit: Geneva Airport.
Purpose
At Geneva Airport, the starting point of our journey was compliance with European standards by replacing our EDS 2 with the brand-new scanners (EDS standard 3) which are more efficient and secure, but also heavier and larger. Our project team faced its first challenge here; the location of the EDS 2 in the airport would not be suitable for this new equipment, and therefore a new structure where those machines could be placed, needed to be built. This new element brought several other problems to light. How do we transfer the bags to the new machines that need to be implemented? Redirecting the baggage flow from one place to another using the old system? Would replacing only a few elements do the trick? The answer is far more complex and extended then yes or no. Implementing a new hold baggage system (HBS) while operating the existing seemed to be complex, but we took the challenge.
An update of all systems meant a replacement of all the existing HBS including check-in counters, sorting and delivery belts. Our airport was (and still is at this date) a major site under construction: buildings needed to be rethought, added or adapted, resources condemned one by one to maintain capacity and major flexibility is demanded.
Commitment
The project team was invited to be part of the day-to-day life of the airport, from check-in to arrivals, from the passenger point of view, from the ground handler point of view, from airlines demands and procedures protocols. Soon, all departments were involved. Safety, operations, engineers, architects, planners, BIM managers, IT, security and more, all devoted to finding the right path to an optimisation both needed and demanded.
The challenge here is making the operational side aware of the infrastructure difficulties and vice-versa. We often transform purpose in routine and commitment in standardisation. Explaining their operational processes and demands gave our teams the opportunity to rethink the processes, question what they do and ask, what could be done differently?
Process
Reconstructing in the same space as we are operating meant that we needed to test if the reconstruction would be achievable regarding the accesses needed to the operational areas of the airport. We replicated the area in one of our car parks and asked the ground handlers to drive on the guided lines with carts and unit load devices (ULDs) and adapted the circulation flow to the needs of the operations before validating the infrastructure demands. These kinds of tests are still used as soon as we encounter a difficulty on the mixed operational and under work area.
Geneva Airport’s ORAT team was involved at the very early stages of the project, right from the study stage”
Commitment from all partners and stakeholders are key to a successful outcome in any project. All changes and losses must be explained, understood, and embraced for the final purpose to be achieved from all parties. Additionally, for that to happen we, as individuals, groups or entities, must focus on the optimisation of the processes. The benefits of this can range from reduction costs, optimisation of resources and more efficient processes. Involving the operations teams, enabling them to make decisions and be part of the process will lead to engagement in the transition, as daily airport operations will be impacted by the different risks and vulnerabilities of what can, and will, happen when bringing a project of this magnitude to life.
Capability
One major asset for a project with this dimension is the ORAT team. Operational Readiness Activation & Transition (ORAT), a mentor between all partners and ultimate decision makers on the process. Operations around the new utilities must be validated, following the transition from old to new, uniting all data from the different partners. We are talking about de-risking operations with a tried and tested methodology of every detail from developing new operational process, facilitating staff training, assuring the viability of the systems, and making sure all parties involved have the knowledge and skills to operate it the right way.
Geneva Airport’s ORAT team was involved at the very early stages of the project, right from the study stage. They helped give shape to the operational plan which traditionally involves a wide variety of groups with diverse interests and priorities (operations, ground handlers, safety, security, infrastructure teams, and more), who must work together to deliver many tasks at critical stages. This specific task and team are the reference when it comes to implementing crucial process that demand structure and leadership to avoid the chaos that can often evolve, steering all parties towards the common end-goal.
They run a series of operational trials repeatedly to fully test and prove all aspects under real life conditions to grow momentum. While replacing the check-in counters and belts e.g., we condemned section by section, making sure that the new ones are fully tested and working before closing the next section. ORAT helped determined if the ground handlers’ agents were fully trained to use the counters and its features, that the maintenance team was trained to solve any technical problems, that the conveyers were responding and successfully connected to the different existing systems and that the bags could successfully travel from check-in to the sorting area. Before all those boxes were ticked, no counters were approved. The same strategies and planning are in place for any or each step of the project to ensure that all processes are respected, understood and applied so the result will be a fully optimised, ready and functional structure that can be operated by all staff.
Learning
As per its definition, learning is the permanent change in behaviour due to direct and indirect experience. Towards the end of this project, we learned that common thinking is often the key to a successful ending, creativity and engineering often work together and that our assets rely on trusting the process more than being bolted to the change. Constantly defying the well-known process by asking the teams to adjust and be proactive when it comes to problem-solving related to a change they didn’t ask for, is often an uncertain thing to do. Adding worksites to their working space, making them work and adjust randomly every other day, colliding with their practices, customs, and behaviours cannot be done if all the stages described before aren’t effectively fulfilled. The purpose must be known, the commitment made, the capability identified so the learning process can begin.
It is common knowledge that a change in behaviour or attitude lies in education, training, and practice. All those items combined result in experience, acquisition of knowledge and skills that are permanent. How did we apply this concept on our day-to-day operational life? By testing, learning, adapting, and by being open-minded of the changes that needed to be made. In addition, gradually, we identified the craving of improvement in all parties involved on the process and implicated on the project. Has this solved every issue on our bumpy road to success? Well, not every single time, but we did learn enough from experiences to be able to identify the weakness and flaws of the project, determine and define the action perimeter, the obligations and responsibilities of every single entity related to the project itself.
Several adjustments were asked of the ground handlers, such as rethinking their workspace. The delivery terminal for example, where every belt needed and needs to be replaced at the exact location of the old ones, demanded a coordination between the terminal agents and infrastructure team. The projects team decided that we needed to replace one belt at the time to be able to absorb the volume of bags expected, whilst being able to make the changes the infrastructure needs to be efficiently operating the new system. This single decision consists of planning, changing the process and procedures, transfer of responsibilities and redistribution of the daily operations. This demands a workflow that must be efficient, flexible, and adjustable so the model that was created can be co-ordinated and repeated when the next belt is condemned.
We are mixing the operational side with the groundwork that needs to be done so both parties need to be co-ordinated while evolving. This dynamic needs also to be organic, flexible, and adaptable – crucial in this specific example as the earlier stages of the project’s implementation had shown that no worksite is identical to the next. So, we learn, and we apply the modifications that are necessary, sometimes despite the planning or deadlines that need to be meet, so operations and infrastructure can co-exist safely and efficiently.
Action
Much work has been done defining the chains of communication (the notorious: who does what?), including timelines, plans, strategic approaches, operational hazards, plan A, B and C. We designated the resources, built the follow-up guidelines, created feedback channels so we could bring updates and optimisations to the next steps, and established the measurements process.
We are now approaching the third year on this project. While we have overcome many challenges, we are only now seeing the depth of the changes that need to be made to successfully achieve the project’s end. For example, because the airport itself is located on the Swiss-French border, we had to close the French section of the airport to do the work and changes that the project demands. That exercise only took several months to be planned and several agreements were made due to the specificity of working in two countries legislations for, and on, the same common ground. At first, it was the belt on arrivals that was condemned but not the check-in area, so the passenger was checked-in on the French side and received his bag on the Swiss side at arrivals, then we closed the check-in area and inversed the process (check-in on the Swiss side and arrivals at French section. At the time of writing, the French sector will be reopening by the end of March 2023, allowing passengers flying to France to register and arrive on the French side of our airport.
How did we manage to work in this organised chaos? We looked at our faults and questioned our practices, we defied our limits and trusted our teams to become accountable and be able to identify and correct all risky situations we could face. We are still aiming for our final goal: a highly sophisticated and efficient baggage logistics centre, where all products and processes will make the job safer, easier, more resourceful and trustworthy. We have one certitude: teamwork makes the project work.
From check-in to gate, from supervision to management, from a multi-national ground company, to a Geneva Airport employee, Sara Branco has more than 10 years of expertise in aviation. Her expertise is required in the challenging project of Implementing a new baggage system compliant with the new security standards.
Issue
Related topics
Airport construction and design, Airport development, Baggage handling, Operational efficiency, Passenger experience and seamless travel, Terminal operations