Paving the way for the A380
- Like
- Digg
- Del
- Tumblr
- VKontakte
- Buffer
- Love This
- Odnoklassniki
- Meneame
- Blogger
- Amazon
- Yahoo Mail
- Gmail
- AOL
- Newsvine
- HackerNews
- Evernote
- MySpace
- Mail.ru
- Viadeo
- Line
- Comments
- Yummly
- SMS
- Viber
- Telegram
- Subscribe
- Skype
- Facebook Messenger
- Kakao
- LiveJournal
- Yammer
- Edgar
- Fintel
- Mix
- Instapaper
- Copy Link
Posted: 17 March 2006 | Cyril Fabre, Pavement Manager, Airbus | No comments yet
In preparation for the increasing introduction of heavy aircraft and new types of landing gear (e.g. B777 and A380), AIRBUS, STBA and LCPC undertook an ambitious research programme to define a more efficient pavement design method.
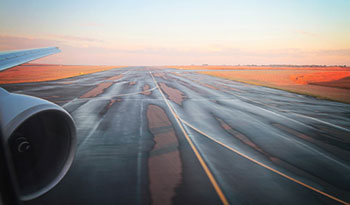
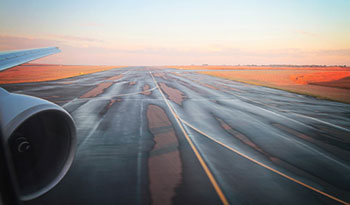
1. Introduction
Full scale pavement testing to optimise and validate A380 landing gear design was started in 1998 at Toulouse-Blagnac Airport in two phases; flexible tests, and rigid pavement tests. New test-validated methodologies are under development, using the software ALIZE to supplement and possibly replace the current Aircraft/Pavement Classification number (ACN/PCN) method, which, although widely used, has limited theoretical basis. The development process calibrates ALIZE results with those from full-scale static and fatigue tests using real aircraft on both flexible and rigid pavements. A380 landing gear configuration, and those of some similar aircraft, were reproduced using a landing gear configuration test vehicle. The results obtained from the test were also validated against production aircraft.
Thirty per cent of A380 targeted airports have rigid runways; therefore a second phase was launched in 2000 using the 3D FEM. A380 landing gear configuration was frozen, and the aim of the tests was to obtain a set of data to improve pavement knowledge and to correlate mathematical models using FEM.
1.2 Airbus strategy
Contrary to the National Airport Pavement Tests Programme (NAPTP), an important P.E.P issue was to be the most representative of real airport conditions. Two experimental pavements were constructed on open field conditions to include the significant influence of external meteorological conditions, and the requirement to subject pavement to real aircraft loads.
2. Flexible tests
2.1 Flexible experimental pavement design
Toulouse-Blagnac airport was selected for laying the specimen pavement as extension to an existing taxiway. The test pavement was 165m long, 30m wide. Each test section was 35m long, separated from the next one by a 5m long “neutral zone”.
Four sections of flexible pavement structures were designed according to the French method for four different subgrade categories: CBR 4, 6, 10, and 15. The test taxiway was built to the current design standard for a B747-400. Structures were made from the same materials and the same thickness for bituminous layers (Bituminous Concrete 8cm, Bituminous Gravel 2*12cm) and the subbase layer had a variable thickness, depending on the subgrade, made from Recombined Humidified Gravel. Three out of four subgrades were found on site (CBR 15, 10, and 6) and the weakest subgrade, CBR 4, was reconstituted with imported material.
2.2 P.E.P Simulator vehicle
A simulation vehicle was manufactured to represent full-scale main landing gear configurations of various wide bodies — A380, A340, 747, 777, MD11 — with up to 22 driven wheels individually loaded up to 32 tons. The vehicle features variable dimensions for bogie position, wheel, and axle spacing.
2.3 Flexible Pavement instrumentation
As loading is symmetrical, each specimen pavement section was instrumented on one side only. Four main resilient strain sensors layers were installed at the top of the subgrade, the bottom of the subbase (GRH), the top of the subbase (GRH), and the bottom of the Bituminous Gravel (GB).
For redundancy, a total of some 250 sensors were installed into the four sections. The separation interval between sensors was greater for the deepest layers, where the wheel grouping effect was expected to induce a larger area of loading influence (subgrade and bottom subbase interval was 60cm)
In the upper layers, the stress diffusion pattern is sharper and restricted to a smaller area around the wheel; therefore sensors were closer together (top subbase and Bituminous Gravel interval is 15cm).
2.4 Static and fatigue tests
- A static campaign to compare and provide information between various a/c with time and spatial correction: 22 configurations were tested in order to support the A380 L/G configuration selection process and provide valuable comparison between the A380 and similar aircraft.
- A fatigue campaign: One configuration tested three a/c (the A380-800F / 777-300 / 747-400) for 5000 coverages with wandering, and nearly 1000 coverages for the high temperature tests. (Three failure criteria were particularly observed: subgrade failure, top subbase rutting, and bituminous concrete rutting and cracking.)
2.5 Data analysis
Of the total of 22 configurations tested, eight were selected taking into account the two following criteria:
- The values of the characteristic bogie parameters (wheel base, wheel track, number wheels and load per wheel) of these 8 configurations must correctly represent the values of these same parameters
- Quality of measurements: the gauges recording the selected configurations must be above reproach, and the entire test parameters during measurement must be correctly controlled.
The results of the strain measurements presented are shown in a final summary intended to facilitate a later numerical simulation. The summary takes into consideration the various bogies that are not interactive in a given configuration.
The rest of this article is restricted - login or subscribe free to access
Why subscribe? Join our growing community of thousands of industry professionals and gain access to:
- bi-monthly issues in print and/or digital format
- case studies, whitepapers, webinars and industry-leading content
- breaking news and features
- our extensive online archive of thousands of articles and years of past issues
- ...And it's all free!
Click here to Subscribe today Login here