Brisbane Airport continues to embrace digital engineering
- Like
- Digg
- Del
- Tumblr
- VKontakte
- Buffer
- Love This
- Odnoklassniki
- Meneame
- Blogger
- Amazon
- Yahoo Mail
- Gmail
- AOL
- Newsvine
- HackerNews
- Evernote
- MySpace
- Mail.ru
- Viadeo
- Line
- Comments
- Yummly
- SMS
- Viber
- Telegram
- Subscribe
- Skype
- Facebook Messenger
- Kakao
- LiveJournal
- Yammer
- Edgar
- Fintel
- Mix
- Instapaper
- Copy Link
Posted: 13 January 2020 | Krishan Tangri | General Manager Assets | Brisbane Airport Corporation | No comments yet
Developments sit in the digital future, but how do we get there? Planned infrastructure usually lies in the rendering of images; training usually depends upon asset availability. But what if all of this could take place in a realm away from reality? Krishan Tangri, GM, Assets at Brisbane Airport Corporation discusses this further.
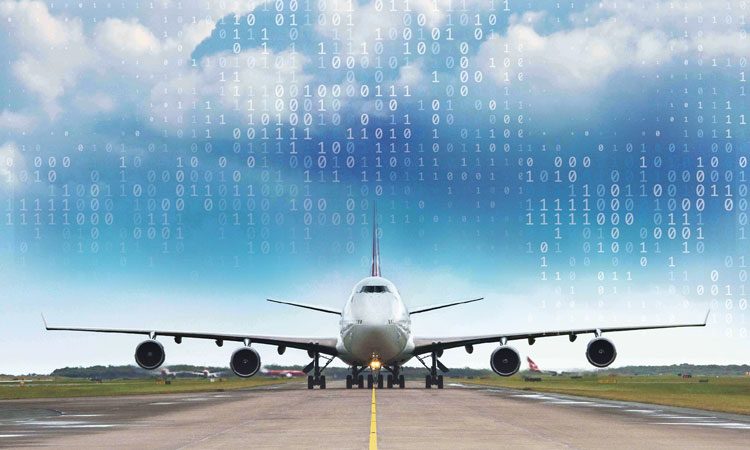
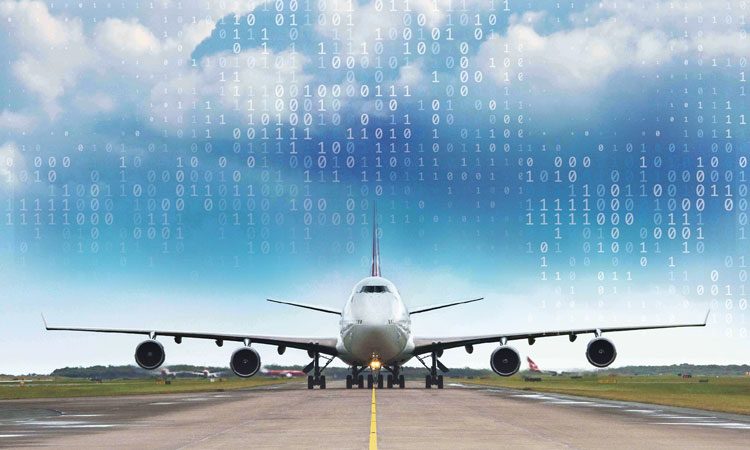
Brisbane Airport (BNE) is Queensland’s most important transport hub and Australia’s third‑busiest airport. Operating 24 hours a day, seven days a week, BNE has two major terminals accommodating 33 airlines flying to 83 domestic and international destinations.
With passenger numbers forecast to more than double by 2034, Brisbane Airport Corporation Pty Limited (BAC) has invested $1.7 billion into building critical infrastructure since 2012, with a further $1.8 billion worth of infrastructure developments scheduled to be delivered between FY18 – FY22.
Digital engineering at BAC
BAC has embraced all facets of digital engineering as “a collaborative way of working to enable more productive methods of planning, designing, constructing, operating and maintaining assets”.
As the airport acts in the role of asset owner, operator and maintainer, it has a strong interest in the ‘whole of asset life’ approach and is focused on adding value at every stage of the asset lifecycle.
In an effort to transition smoothly to a full digital engineering environment, BNE has examined the challenges it faces in the context of a fully operational international airport, a semi‑mature local supply chain, strong legacy systems still in place since privatisation in 1997, variable skillsets of current staff, quality standards and protocols to be adopted, with the over‑riding desire to be able to demonstrate ‘value added’ and a balance between new technology and the achievement of tangible benefits over a non‑digital engineering approach.
Faced with multiple opportunities across the full spectrum of infrastructure development, the airport has utilised and harnessed the benefits of various digital technologies.
Laser scanning technology
This technology has been employed successfully in the survey of existing assets, particularly complex plant room areas and previously unchartered building services. The resultant point cloud file is then transferred into a working, rendered parametric file suitable for use by designers and contractors as an accurate base for any proposed upgrade.
Either the point cloud model or the accompanying rendered parametric file can be navigated in viewing programmes to gain an understanding of the ‘as‑built’ conditions.
Significant time savings have been achieved by using point cloud laser surveys when compared to older methods of measurement. The production of 3D parametric files suitable to accept material or product meta‑data is another major benefit.
Programme (4D) and cost (5D)
To extract maximum benefit from the production of 3D BIM files, BAC has developed the ability to link the meta‑data from the design files to both programming (4D) and cost (5D) applications. Although further work is required around the issue of unique identifiers, encouraging results have been achieved.
Use of real‑time information allows all participants (asset owner, designers, consultants including quantity surveyors and programmers and contractors) to visualise the progress of construction activities and related costs over the progress of the projects. BAC is working toward an industry‑wide protocol that can be utilised across the portfolio of projects, regardless of the originating native file type.
Virtual reality
With its recently commissioned Demonstrator Room, BAC is now capable of reaping the benefits of its virtual reality arrangement, particularly in the area of project fly throughs, visualisations and 3D renderings for the benefit of all stakeholders.
Our finding is that project sponsors and stakeholders, whether an internal client department, an external tenant, executive leadership team or the general public, all have one thing in common and that is the desire for clearer, more interactive, more realistic visualisations of the final product. With an emphasis on customer experience throughout the airport’s terminals, the VR arrangement has become a valuable tool to bring all stakeholders closer to the design in the early stages of design, where constructive suggestions can be incorporated without compromising the delivery of construction documentation.
VR case study 1 – wayfinding and signage
Using a digital 3D model, BAC was able to create a virtual wayfinding experience where the key stakeholders – operations, public transport operators, rental car operators and parking/ transport operators – were given VR headsets to view new wayfinding paths through the upgraded passenger sky‑bridge leading to and from the domestic terminal. This VR tool allowed the stakeholders to be immersed in the new environment, allowing them to explore the different options to be experienced by passengers on both inbound and outbound journeys and modify and prototype in real time, thus ensuring their input into the final design. This increased collaboration and communication benefited BAC and the commercial stakeholders, ensuring that expectations of the result were clearly understood and accepted.
VR case study 2 – airside driver training
With BNE’s new runway set to be commissioned in mid‑2020, a strong need has emerged for the training and re‑training for multiple airside drivers to understand the new layouts of roads, taxiways, aprons and aircraft parking positions.
This is being achieved by the development of an interactive airside ‘driving simulator’ tool specifically tailored around the new arrangements and features the incorporation of the new road network, airside signage, proposed aircraft movements, prevailing weather conditions, airside lighting, day evening and night time visibility and FOD.
The power of this simulator sits with the completeness of the digital environment in which the user finds themselves immersed. The environment was created from 3D BIM models, aerial imagery, GIS data and gaming engines to add in aircraft, weather, FOD and the driver’s dashboard imagery, all whilst sitting in a realistic vehicle driver’s console.
The benefits are numerous. The training is happening now, long before the physical asset is commissioned. All drivers will be trained, ready and licensed on day one, rather than having to wait.
BAC envisage this VR tool to be of ongoing benefit when new contractors/ drivers require initial training before being licensed to drive airside.
Augmented reality
Combining real‑world imagery with scaled, computer‑generated 3D images to enhance the viewers’ experience is a very powerful visualisation tool which has found multiple applications at Brisbane Airport.
The idea of overlaying 3D digital imagery over photographs of the existing view to generate a unified and enhanced view of the end product, in its simplest form, provides earlier and more detailed visualisation which generally leads to more informed and accurate decision making.
When further enhanced with the introduction of sound and touch, augmented reality really starts to make the viewer question what is real and what is not.
AR case study – international terminal expansion
In 2017, BNE embarked on an international terminal expansion project to accommodate increasing aircraft gate demand.
The architects were challenged to produce a series of three AR images which were to describe the current building, the proposed development and then the ultimate solution for the future.
The provision of these images, which clearly blurred the lines of what is real and what is not, helped all stakeholders understand the logic of the mid‑term development and the prospect of future seamless ultimate expansion when required. It was very simple but effective.
The benefits of using technology
Digital engineering, including the aspects of VR and AR, has brought benefits to BNE when analysed on the ‘whole lifecycle’. Capital cost efficiencies have been realised through a reduction in unbudgeted variations, reduced contract sums because of less unknown risks at tender, coordination issues being resolved during design phase rather than onsite and improved accuracy of cost estimates earlier in the process.
Time benefits have been realised through reduced design review and approval periods, shorter design periods, increased offsite manufacture and improved stakeholder engagement through clearer visualisations.
Quality improvements have been achieved from off‑site manufacture, greater and more effective coordination and fewer non‑conformances due to improved discipline coordination.
Safety improvements have been significant from the use of VR equipment in safety briefings, toolbox talks and site inductions. Better visual representation of construction elements and site conditions have provided improved interface control and clearer stakeholder understanding.
Optimisation of designs to increase energy efficiency, reduce water wastage and minimise waste have contributed significantly to BNE’s environmental and ESD targets.
Using the 3D BIM model and VR to mitigate project risks around staging, disruption and business continuity, passenger experience has proven to be highly beneficial.
Looking ahead to the next steps
Now that the ‘value added’ has been assessed, BAC is looking to the next steps on the digital engineering journey. Of all things, we see the need to establish the ‘central point of truth’ as the most powerful and necessary element to be instigated. To achieve this goal, a dedicated digital engineering server is contemplated, equipped with appropriate permissions and access protocols. All information will reside within and be available for multiple departments including finance (for the asset register and depreciation schedules), operations (for up‑to‑date working information and data relating to the asset base), facilities (to extract all meta‑data for use in the CMMS maintenance platform, including warranty information), CAD and spatial data (to generate the airport digital twin and retain all of the as‑built information for future reference).
Further progress is planned in the VR area, particularly in relation to scenario testing (optioneering), operational training in the virtual environment (emergency response) and safety (virtual walkthroughs, evaluations and checking).
Linking of 3D BIM data, BIM geometry, in ground GIS data, photography and asset data to provide AR images both in the office and in the field presents further opportunity to extract benefits from the whole of the digital engineering initiative.
Embracing digital engineering
The transition to digital engineering, including both VR and AR is an ongoing process but BNE is determined to harness the benefits in such a way that it brings benefits to all stakeholders, from the design process, stakeholder management, financial data analysis, facilities management, contractors, the supply chain and ultimately BNE as the asset owner, operator and maintainer.
Results to date have been encouraging. The two pilot projects undertaken have returned an average ‘value added’ of 12.5 per cent over the design and construction phases. Further assessment is yet to be undertaken for the handover, commissioning, maintenance phase but the signs are positive.
It is clear that digital engineering is becoming business as usual at Brisbane Airport and the corporation takes pride in having developed a skill base to further develop the benefits of this advancing digital technology.
Biography
Issue
Related topics
Airside operations, Augmented reality (AR)/ Virtual reality (VR), Sensory technology, Terminal operations