Designing an airport to be more than just a gateway
- Like
- Digg
- Del
- Tumblr
- VKontakte
- Buffer
- Love This
- Odnoklassniki
- Meneame
- Blogger
- Amazon
- Yahoo Mail
- Gmail
- AOL
- Newsvine
- HackerNews
- Evernote
- MySpace
- Mail.ru
- Viadeo
- Line
- Comments
- Yummly
- SMS
- Viber
- Telegram
- Subscribe
- Skype
- Facebook Messenger
- Kakao
- LiveJournal
- Yammer
- Edgar
- Fintel
- Mix
- Instapaper
- Copy Link
Posted: 4 September 2019 | Cristobal Correa - BuroHappold Engineering | No comments yet
Jewel Changi is not just a functional airport building, designed to move people through quickly so they can reach their destination. It was designed to be the destination.
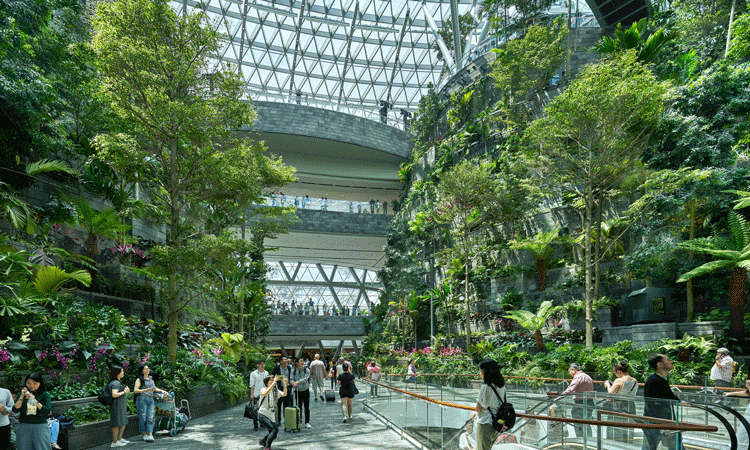
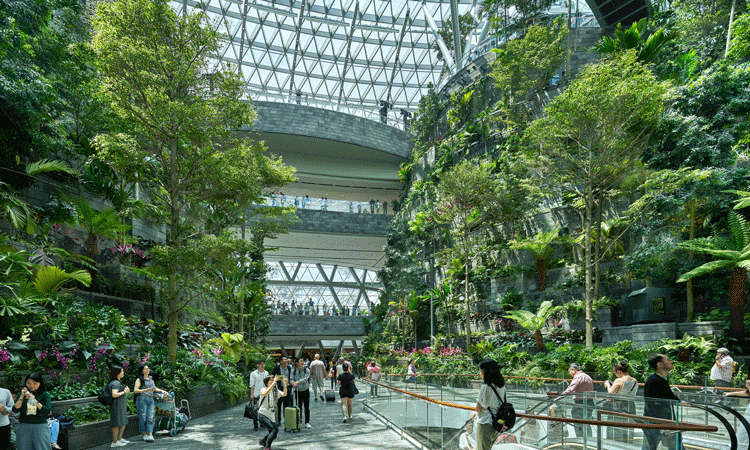
Photo credit: Timothy Hursley
Even for the world’s most popular airports, competition is growing. Innovation thrives in the sector and whether this means a new terminal or small retail area, everything is carefully crafted to make the passenger experience both convenient and enjoyable. In an era with ever-growing choice, it’s a buyers’ market – and airport owners know their offerings and design must stand out.
Even Changi Airport, one of the most popular stop-over destinations, has not escaped this. Despite being voted the world’s best airport by passengers for the last seven years, its owners knew it had to innovate to retain its position as a prime stop-over airport amid fierce competition from other destinations in southeast Asia. At the core of its strategy to manage this is Jewel – a unique new structure at the heart of the airport, that opened earlier in 2019.
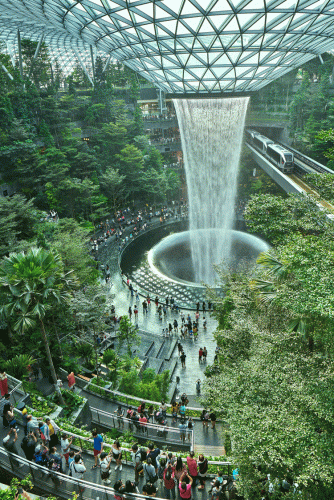
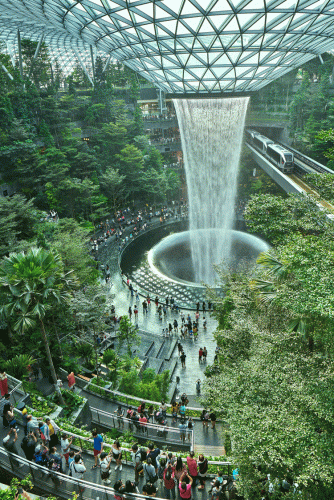
Photo credit: Timothy Hursley
From the outset, the aim was to make the new building breath taking. After all, an airport is a country’s front door. It is both the first and last memory travellers will have of a place, and with competition growing, it needs to be memorable itself.
The beauty of the project and variety of amenities within it are, of course, central to this. Featuring a 5.6-acre garden, retail outlets, accommodation and leisure destinations and the largest indoor waterfall in the world, Jewel’s amenities are located landside. Those who are travelling can check in their baggage then spend the day in Jewel, joined by local people. It’s not just aimed at travellers, but also at day-trippers from Singapore. Before thinking about the amenities, however, job number one was to make the structure itself as awe-inspiring as possible.
The initial sketches produced by Safdie Architects showed how this could be achieved. People descending from the skies over Singapore or looking up from the ground would see a vast, transparent façade, rising uniformly from the ground and curving inwards as it reaches the summit. There it gives way to an oculus at its centre – a 12m opening at the apex of the real jewel of Jewel Changi – the 40m indoor waterfall, dubbed the ‘Rain Vortex’.
This aspirational design could not have been made a reality even five years ago. The most advanced computational technology has supplemented highly-advanced engineering methods to bring about such a ground-breaking proposal. If achieved, the project team knew it would be truly one-of-a-kind. Solving the substantial engineering challenges involved fell to BuroHappold working alongside Safdie.
The roof structure – breaking new ground in gridshell design
Primarily, a solution which allowed this apparently seamless design to take shape over such a vast area had to be found. To make the roof design work it needed to be broken down into thousands of smaller components. Nearly 10,000 unique, triangular glass panels are connected by 14,000 steel elements and more than 5,000 nodes.
Glass was chosen as a logical material to deliver the transparent effect, but this had to be properly supported across the approximately 200m roof. An efficient way of doing this is with a gridshell, which is known as a strong and efficient way to span long distances, but Jewel goes beyond what has been achieved before. At 210x156m it is the world’s largest gridshell enclosed building. While the gridshell covers the roof area only, the rest of the façade is designed to look the same, with the effect continuing down to the ground.
This process wouldn’t have been possible without advanced building modelling software to plan and monitor the structure’s development. Building information modelling (BIM) was used throughout the planning and construction stages to create digital plans of the construction process, tracking each component individually and ensuring that everything was put together in the right order, assuring structural integrity and protecting the architects’ vision. It also meant key issues normally dealt with later in the process were addressed at an early design phase. Materials, construction processes and detailed design frameworks were all considered as part of this preparatory work, showing clients and contractors alike that the intricate design could be achieved safely.
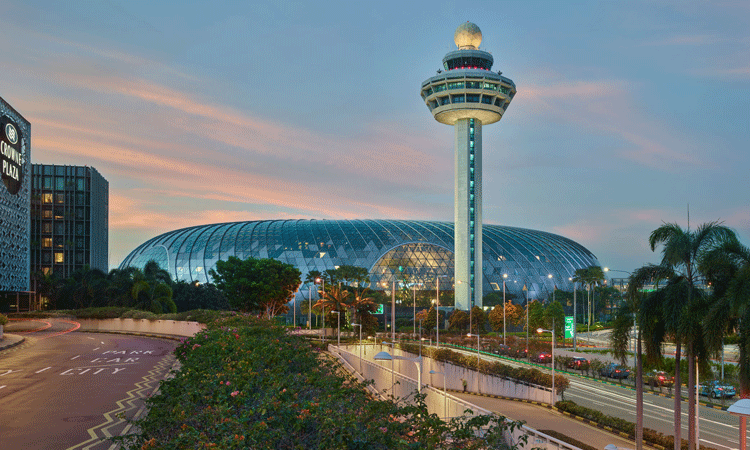
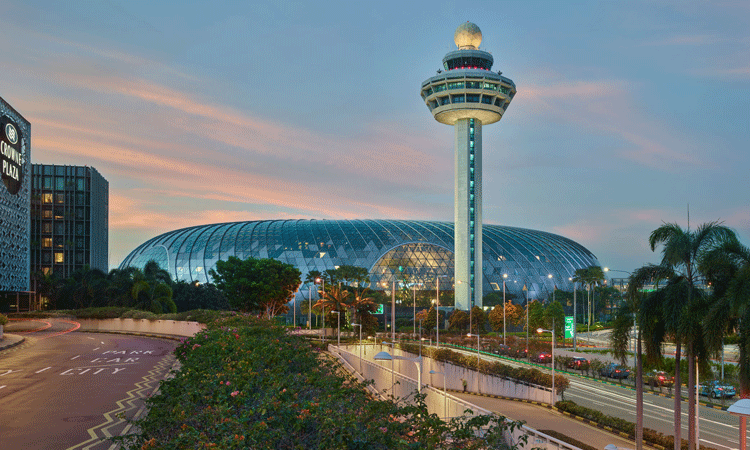
Photo credit: Timothy Hursley
The location of an existing skytrain below, running passengers between terminals, required a further modification to the roof design. If the oculus was positioned exactly in the centre, water was at risk of falling onto the train. To avoid this, a slightly asymmetrical design was prepared to position it slightly off centre. This need for asymmetry means that each panel and node is unique, fitting into one specific space in the roof. Advanced 3D-printing technologies were used to manufacture each element to exacting specifications – panels are in a variety of sizes and each node connects to a panel at different points.
BIM again came to the fore when making this feasible. Every piece then had to be put in exactly the right place in exactly the right order during construction – 26,000 connection points creating a giant 3D jigsaw puzzle. BIM identified and tracked each panel by its own QR code, ensuring accuracy when putting them in place. The digital organisation was essential to ensure the final structure fitted together.
A nearly column-free design
The transparency of the building was to bring in as much natural light as possible, something which was at the heart of the design. The interior has more than 2,000 trees and over 100,000 shrubs – with the garden design having to account for the areas where shadows would be cast.
However, when talking about a façade of over 27,000 square metres, weighing over 6,000 tonnes, a strong supporting structure needed to be put in place. A method of doing this had to be devised without negating the aesthetic effect the glass façade brings. Those inside had to be able to see the light beyond the tops of the trees – not the shadows wrought by columns marching across the gardens.
A solution was found using 14 steel ‘tree’ columns, positioned in key areas around the perimeter. Each of these have four trunks coming off it, adding additional support. These tree columns and supports were put in place first during construction. The span of the roof required a staggered building process, splitting it into 10 pie-shaped parts and constructing them one by one. For each, the gridshell was erected from the columns, with work on the glass panels following several sections behind.
The Rain Vortex
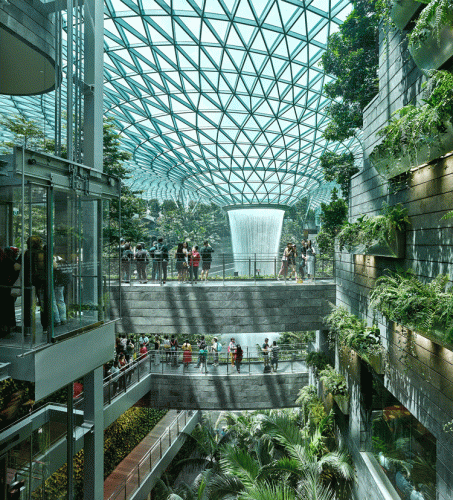
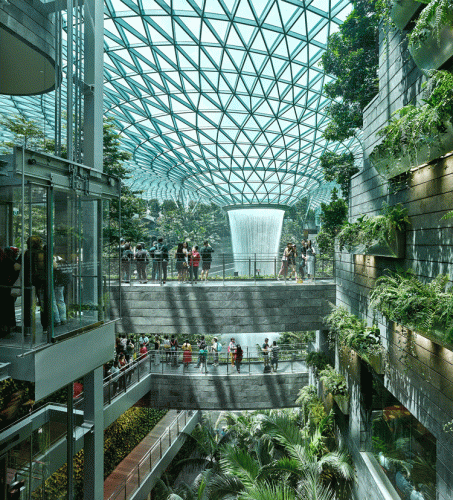
Photo credit: Timothy Hursley
The most striking feature of the façade, the ‘Rain Vortex’, flows from a 12m opening in the roof. With a flow capable of reaching 10,000 gallons per minute in heavy storms, the 40m waterfall is fed by pipes built into the façade, supplemented by rainwater which is drawn towards the oculus. After cascading down to the pool below, the water is transported around Jewel through the pipes, allowing it to be reused both in the waterfall and as irrigation in the surrounding gardens.
For the engineering team, the storage of such large amounts of water needed to be done in such a way that there was no danger of weakening the structure. The curved design of the roof was implemented to avoid water pooling and subsequent concerns about additional weight on the structure – all areas of the roof have a two per cent slope or more to ensure excess finds its way to the oculus.
Building around existing operations safely
The construction of Jewel was remarkable in itself – using cutting-edge engineering to push the boundaries of modern design. This would be true regardless of where it was located, but the final, continual, challenge was its position at the heart of Changi. Jewel was allocated for development on the site of a former open-air car park at Changi Airport, between existing terminals. The construction process had to seamlessly connect to Changi’s terminals, in addition to public transport routes. This all had to be done without disrupting the airport’s existing operations.
One tricky element of this was how the glass façade took shape, both during and after construction. Tests were carried out to ensure the glass façade was not constructed in a way which light could distract nearby air traffic controllers. Again, the curvature of the roof was part of the solution to ease potential concerns over this, with shape modification in certain places ensuring the gridshell is out of the radar horizon of air traffic control.
More than a gateway
For airports to continue to compete, they need to see themselves as more than just a gateway – in the future they will seek to attract both passengers and locals on their own merits. Jewel Changi embodies this emerging truth in the aviation industry. For the 85 million people estimated to visit each year, they won’t just go to travel. They’ll go to walk through the gardens, stand by the waterfall and look up at the sky.
Related topics
Airport cities, Airport construction and design, Passenger experience and seamless travel, Sustainability