Improving runway safety
- Like
- Digg
- Del
- Tumblr
- VKontakte
- Buffer
- Love This
- Odnoklassniki
- Meneame
- Blogger
- Amazon
- Yahoo Mail
- Gmail
- AOL
- Newsvine
- HackerNews
- Evernote
- MySpace
- Mail.ru
- Viadeo
- Line
- Comments
- Yummly
- SMS
- Viber
- Telegram
- Subscribe
- Skype
- Facebook Messenger
- Kakao
- LiveJournal
- Yammer
- Edgar
- Fintel
- Mix
- Instapaper
- Copy Link
Posted: 13 December 2014 | Joshua Polston | No comments yet
Eight years in the making, Oakland International Airport has now completed its runway safety area upgrade programme. Senior Aviation Project Manager, Joshua Polston, provides an overview
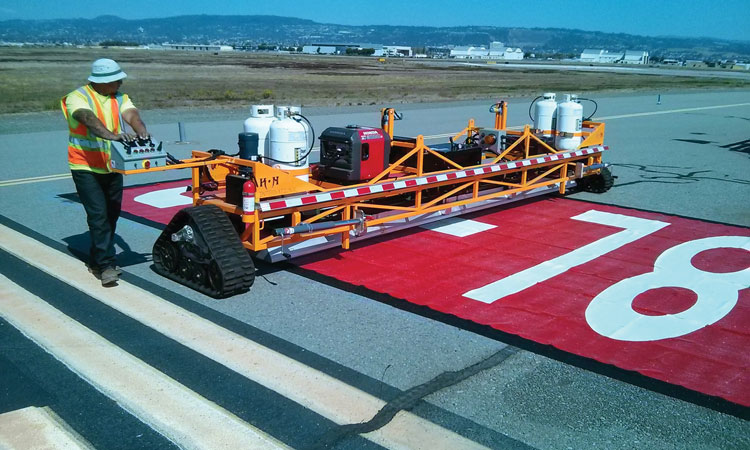
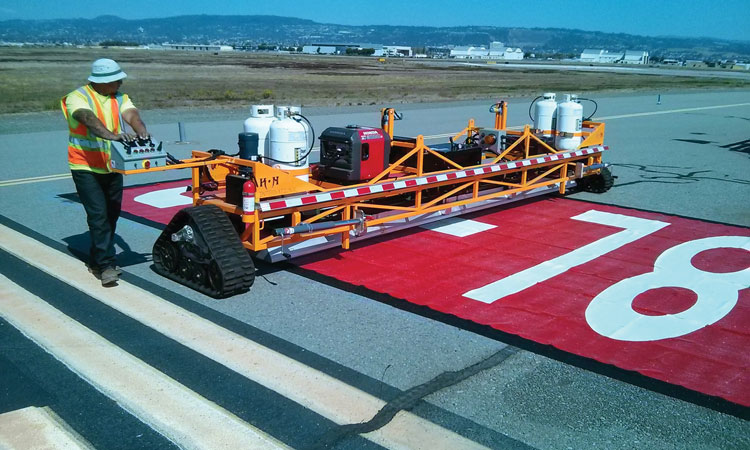
How do you rebuild a watch while it’s still running? The answer is with great difficulty! Such was the challenge to fully meet all Runway Safety Area (RSA) standards for Runway 12/30 at Oakland International Airport (OAK). Like all Part 139 certificated airports in the United States, OAK has been working to upgrade the RSA at the airport. Adding to the challenge at OAK is the fact it must serve all of the air and cargo carriers from a single runway. In 1999, the FAA published renewed guidance on how airports may meet standard RSA requirements. This effort was given additional weight when, in 2005, Congress specifically required all airports to meet the standards by the end of 2015 as part of PUBLIC LAW 109–115.
OAK’s south airfield was built in the late 1950s; prior to the current crop of RSA standards that are intended to give pilots additional safety areas should they overshoot or veer off a runway. RSAs must extend 1,000ft beyond runway thresholds and cover 250ft on either side of the runway centreline. Many airports around the country are landlocked and/or bounded by water bodies such as Oakland.
The challenge at OAK extends beyond a lack of real estate, though. OAK began studying RSA improvement strategies in 2005 with an initial conceptual study report that looked at seven options for compliance and assessed those against the financial criteria set out by the FAA in Order 5200.9, which established a maximum practicable budget of $30 million per runway. The San Francisco Bay borders the airport on three sides preventing easy expansion and is also protected by a state agency that severely limits any new fill into the Bay. To achieve full dimensional RSA compliance, the airport would need to extend the airfield 600ft into the Bay, but such an extension would have exposed the project to extreme schedule risk from legal challenge in the environmentally conscious Bay area community.
Since the most straightforward San Francisco Bay fill approach was off the table, the airport looked at other practicable alternatives and settled on a non-standard engineered material arresting system (EMAS) similar to a runaway truck ramp for planes. The EMAS was reviewed by the FAA and accepted as the preferred solution. One problem with the EMAS is that due to the constrained real estate, it was not long enough to stop a B747, which is the design aircraft for Runway 12/30. After two years pursuing the EMAS option, the FAA asked the airport to re-evaluate options for full compliance with RSA standards. The preferred alternative at the end of the study was for a combination of declared distances and relocating the threshold 520ft to the north west. Along with these changes the estimated project costs increased from approximately $30 to $60 million.
In addition to San Francisco Bay surrounding the airport, many of the low lying lands on the airfield are considered by the U.S. Army Corps of Engineers to be environmentally sensitive wetland habitat. Since there is habitat, the U.S. Fish and Wildlife Service assumes there are also endangered species on the airport property; in essence a one-two punch. To complete the RSA improvements on the airfield required fill or disturbance of 14 acres of wetlands at a mitigated cost of over $8 million.
The new design increased costs for the project because it introduced a much higher level of complexity; shifting both runway thresholds and adding two new taxiways to mark the new ends of the runway. Remember our initial watch analogy: not only did the gears need to be replaced but the numbers on the faceplate are shifting at the same time. The project engineers developed a revised bid estimate of $26 million.
The contractor bids ranged from $35 to $42 million; all in excess of the project budget authorisation. OAK had a serious problem and the 2015 deadline was not considered a flexible date by the FAA. After receiving higher bids the airport had no choice but to reject all bids and go back to the drawing board.
OAK took a look at the scope and performed some value engineering triage, removing paving scope, simplifying the phasing and looking to give the contractor a window larger than four hours per week to completely shut the runway. The airport also went back to the Port Board of Directors to request additional authorisation to award bids of up to $37 million. The scope tweaks and value engineering produced a new low bid of $33 million and the project began construction in May 2013.
The scope of work could be divided into three distinct sets:
- Civil and paving
- NAVAIDS and flight procedures
- Electrical, lighting, and VISAIDS.
The civil work on the RSA covered all the earthwork and new paving. Prior to the project, Runway 12/30 had three high-speed and two standard taxiways providing access. As part of this project, the former taxiways U, W, Y, V, were renamed with the addition of two new standard taxiways for a clean set of taxiway location names from W1 to W7. Extensive grading and drainage work was also undertaken to provide clear frenzel zones for the Instrument Landing System (ILS) Glideslope antennas and to channel water away from the airfield.
Due to the shifting thresholds at both ends of the runway, all of the NAVAIDS and flight instrument procedures were modified for the re-configured runway. The most significant change on the airfield from an air traffic control and user’s perspective is the relocation of the Runway 12 Glideslope to the west side of the airfield. The prior antenna had been improperly sited in a very inefficient location causing pilots to often see signal deviations on final approach to Runway 12 due to ground interference. The FAA Tower also needed to stage aircraft far away from the threshold to keep them out of the ILS critical area for as long as possible, significantly adding to delay during southeast weather operations.
During this whole affair, the magnetic variation of the earth shifted to bump the runway up to the next 10-degree digit and on 17 October 2013, the runway was re-named 12/30 (from the prior 11/29).
While the civil and NAVIAD work was extensive, the construction of airfield electrical, lighting, and VISAIDS represented the majority of work from a project budget standpoint. The shifting positions of the thresholds and the age/condition of the current system dictated that nearly all airfield lighting elements were replaced, modified, or demolished. This extensive work encompassed three major areas:
- VISAIDS for aircraft operations
- Pavement lighting and signage
- Surface Movement Guidance System (SMGCS) improvements.
This work was also coordinated with a parallel FAA project to replace all of the electrical infrastructures on the airfield, which was more than 60 years old.
OAK offers CAT III ILS on Runway 30 and CAT I on Runway 12. Supporting this capability is an ALSF II lighting system on Runway 30 and a MALSR system respectively. Due to the shift of threshold, the system required modification to shift the stations for the proper intervals. This required new wiring and conduit throughout the structure to replace infrastructure that was too old to modify. Same for the MALSR on Runway 12 which due to exposure to the marine environment, required complete replacement.
With the new taxiways and shifted runway, many of the taxiway and runway lights required relocation and upgrades. Due to the magnetic variation changes and taxiway re-naming nomenclature, all of the lighted airfield signs needed to be replaced with new bases and panels. These significant modifications are summarised in.
As a CAT III B certificated airport, OAK began working on a Surface Movement Guidance System (SMGCS) 15 years ago to add an additional layer of safety to the airfield during low visibility operations (LVO). The system, based on ALSTOM equipment, had never been fully commissioned by the airport and was using antiquated UNIX-based servers to manage the hundreds of individual smart-switch fixtures. The system was becoming more and more fragile over time and spare workstations were no longer available from the manufacturer. After a number of the spare Unix workstations failed, the airport had no choice other than to seek used workstations on eBay to keep the lighting system operational. After performing a cost/benefit analysis, it was shown that completely removing the old system and starting from scratch would be more cost-effective that trying to source and reprogram the current, dated, equipment.
A new SMGCS system was designed and installed using ADB hardware and fixtures. The new system has greatly simplified maintenance and uses only one set of power cables for both electrical load and system communications, thereby eliminating an entire network of dedicated communications cables. The airport maintenance department is also excited to have domestically sourced spares and equipment to keep the system up and running. The prior system’s light fixtures required a lengthy maintenance lead time as malfunctioning equipment required transport back to the UK for refurbishment. This added considerable time and cost to maintain system components.
One innovative feature of the new SMGCS system was implemented on the three zipper roads crossing taxiways Bravo and Tango. The LVO operating manual requires airports to shut down all zipper roads when the SMGCS system is activated. This requirement would add additional duties to the Airside Operations Department at a time when they need to devote all resources to keeping the airfield safe for Airport users. The RSA design and construction team developed a solution using the SMGCS system to automate the closure of the roads. During LVO operations, three in-ground lights on each end of the zipper road switch to solid red, closing the road. During normal operations they are flashing amber, providing additional visual cues to drivers about to cross an active taxiway.
In all, the RSA programme at OAK was over eight years in the making and, in October 2014, was substantially complete.
Biography
Joshua Polston has served as Senior Aviation Project Manager at Oakland International Airport since 2006. His background includes transportation planning, finance, and economic analysis. Prior to joining Oakland, Joshua worked with Booz Allen Hamilton Consultancy and San Francisco International Airport. A graduate of UC Berkeley, he currently serves as faculty at Laney College, teaching macroeconomics.
Issue
Related topics
Airside operations, Foreign object detection (FOD), Regulation and Legislation, Runways and pavements, Safety, Terminal operations