Stansted Airport completes £70 million baggage system upgrade
- Like
- Digg
- Del
- Tumblr
- VKontakte
- Buffer
- Love This
- Odnoklassniki
- Meneame
- Blogger
- Amazon
- Yahoo Mail
- Gmail
- AOL
- Newsvine
- HackerNews
- Evernote
- MySpace
- Mail.ru
- Viadeo
- Line
- Comments
- Yummly
- SMS
- Viber
- Telegram
- Subscribe
- Skype
- Facebook Messenger
- Kakao
- LiveJournal
- Yammer
- Edgar
- Fintel
- Mix
- Instapaper
- Copy Link
Posted: 25 May 2021 | International Airport Review | No comments yet
Stansted’s baggage system upgrade, which has taken four years to complete, was completed ahead of schedule as a result of the COVID-19 pandemic.
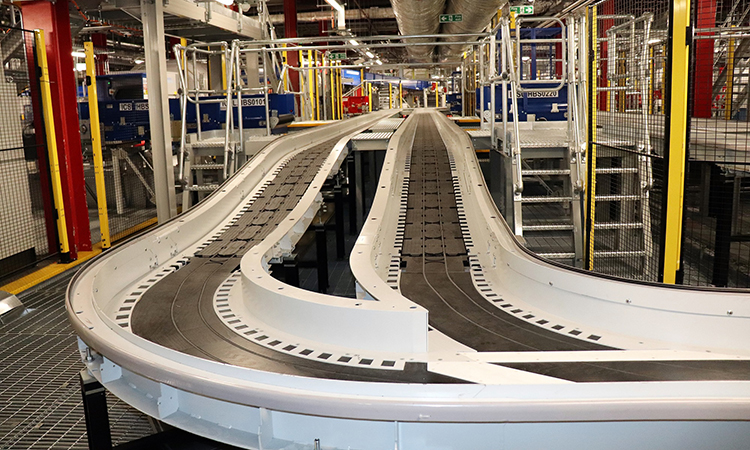
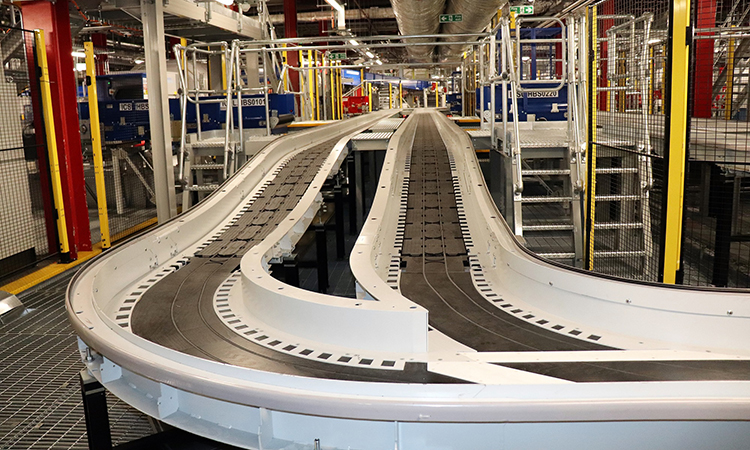
Credit: London Stansted Airport
The COVID-19 pandemic may have brought airports to a standstill, but, beneath London Stansted Airport’s (STN) terminal, a £70 million baggage system renovation has been driven to the finish line.
The project, which has taken four years to complete, is the largest upgrade to Stansted Airport’s baggage network since the terminal opened in 1991. It involved replacing the ageing set-up of conveyor belts and chutes with 2.4km of track and 180 automated carts.
Designed by Beumer Group, the new low energy, fully automated system is faster and more efficient than the one it replaces. It is the longest system of its type in the world and, at speeds of up to five metres per second, bags will take around six minutes to travel from check-in to being ready to load onto an aircraft.
Steve Radford, Hold Baggage System Programme Lead at Stansted Airport, who oversaw the project, said: “We’re delighted to reach this very important milestone in the hold baggage system project. While passengers simply hand their baggage in at check-in for their journey, below the terminal is a highly automated and complex system that seamlessly and safely ensures that the right bag reaches the right flight. The Beumer autover® system uses the latest digital technology, which will future-proof London Stansted’s baggage operation for years to come, improving performance for both our passengers and airlines.”
The work was initially carried out in stages to minimise disruption. However, the drop in traffic because of the coronavirus pandemic meant that the airport could speed up the project and complete it ahead of schedule.
“We would much rather have welcomed the numbers of passengers that we were expecting, but, under the circumstances, the team took advantage of the situation and did a brilliant job. Despite the challenges that we’ve all faced in the last 12 months, it’s been encouraging to work on a project that’s going to have such a positive impact on passengers when they return to the airport,” added Radford.
The work also included linking the new system with a new check-in area that opened in 2019 and the installation of new hi-tech ‘Standard 3’ baggage scanners, which are required under new European Union (EU) regulations.
Related topics
Airside operations, Baggage handling, COVID-19, Machinery, Terminal operations